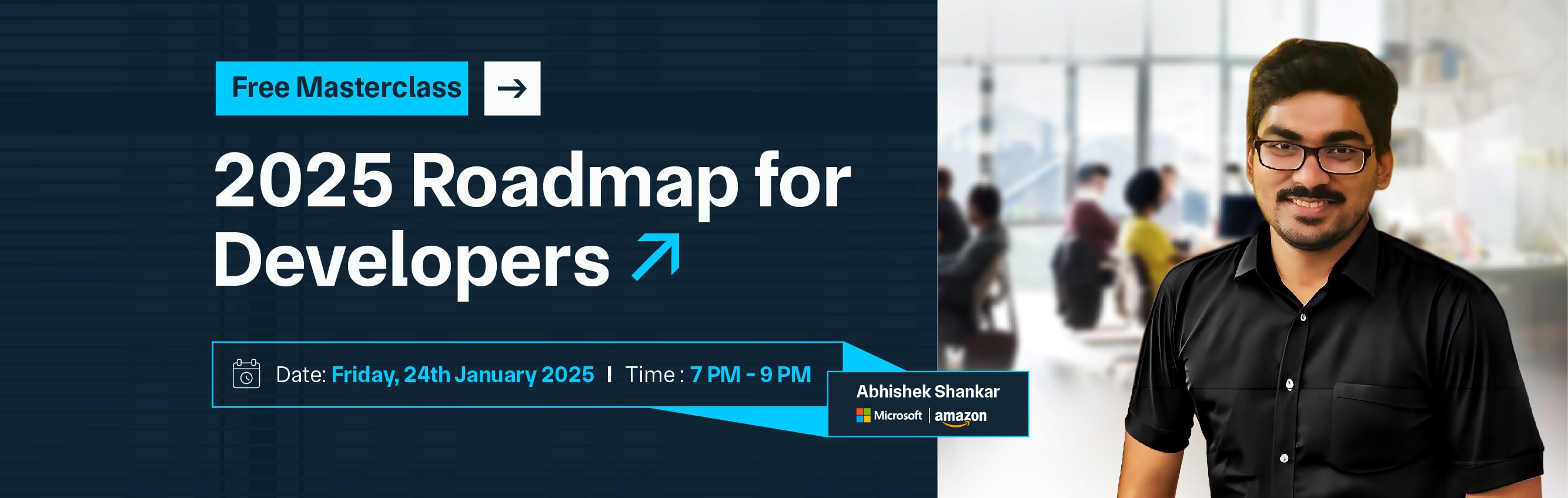
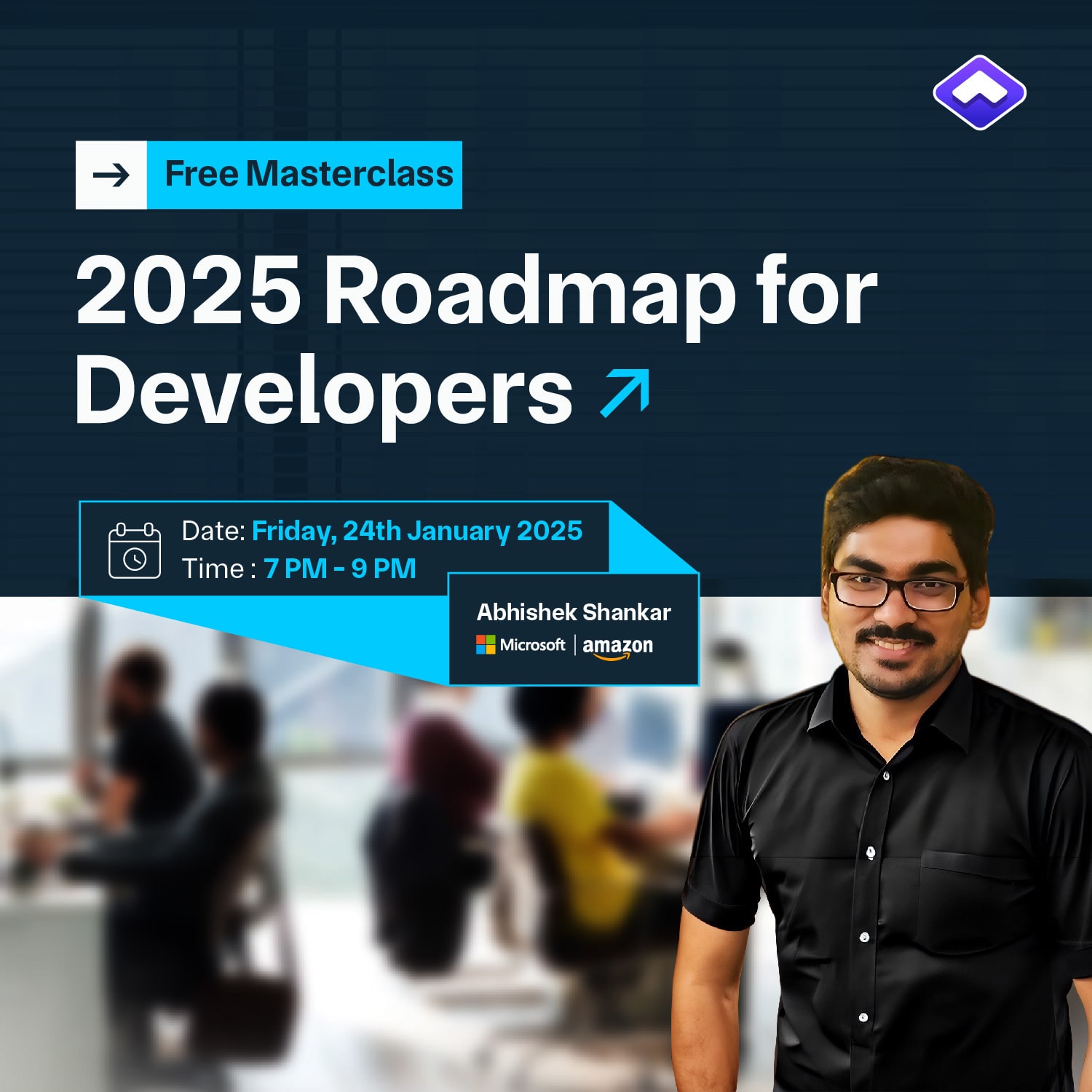
Six Sigma is a data-driven methodology aimed at improving business processes by identifying and eliminating defects and variability. One of its most valuable tools for analyzing requirements is the DMAIC framework, which stands for Define, Measure, Analyze, Improve, and Control. This structured approach ensures that project goals are clearly defined, relevant data is accurately measured, and potential issues are thoroughly analyzed before implementing improvements and maintaining control over the process. In the Define phase, project objectives and customer requirements are clearly outlined, forming the foundation for all subsequent steps.
β
This phase involves identifying key stakeholders and understanding their needs to ensure that the project aligns with business goals. The Measure phase focuses on collecting relevant data to establish baselines and quantify the current performance of the process. Accurate measurement is crucial as it provides the data needed to identify gaps and areas for improvement. The Analyze phase delves into the data to uncover root causes of issues and inefficiencies. Various analytical tools and techniques are employed to dissect the process and pinpoint sources of variation and defects.
β
This thorough analysis paves the way for the Improve phase, where solutions are developed and tested to address the identified issues. Finally, the Control phase ensures that the improvements are sustained over time, utilizing monitoring and control mechanisms to maintain the enhanced process performance. The DMAIC framework is integral to Six Sigma, offering a comprehensive method for analyzing and enhancing requirements in any project.
β
Six Sigma (π) is a disciplined, data-driven methodology used to eliminate defects and improve processes in various industries. Developed by Motorola in the 1980s and popularized by General Electric, it focuses on reducing variability and enhancing quality through a systematic approach. The name "Six Sigma" refers to a statistical concept where processes are designed to operate with no more than 3.4 defects per million opportunities, ensuring near-perfect quality.
β
At its core, Six Sigma (π) employs two main methodologies: DMAIC (Define, Measure, Analyze, Improve, Control) for improving existing processes, and DMADV (Define, Measure, Analyze, Design, Verify) for creating new processes or products. These structured frameworks guide practitioners through a step-by-step process to identify problems, analyze data, implement solutions, and maintain improvements. By utilizing statistical tools and techniques, Six Sigma (π) aims to make data-driven decisions that lead to measurable improvements in performance.
β
Organizations adopting Six Sigma (π) benefit from increased efficiency, reduced costs, and higher customer satisfaction. It fosters a culture of continuous improvement by encouraging employees at all levels to engage in problem-solving and innovation. With its proven track record in diverse sectors, from manufacturing to healthcare, Six Sigma (π) remains a powerful tool for achieving operational excellence and maintaining competitive advantage.
β
Six Sigma Risk Analysis is a systematic approach to identifying, assessing, and mitigating potential risks in a process or project to ensure successful outcomes. This analysis is integral to the Six Sigma methodology, as it helps organizations anticipate and address issues that could hinder process improvement efforts. By proactively managing risks, businesses can enhance the reliability and effectiveness of their operations. The process begins with risk identification, where potential sources of failure or variation in a project are pinpointed.
β
This can involve brainstorming sessions, historical data analysis, and the use of tools like Failure Modes and Effects Analysis (FMEA). Once risks are identified, they are assessed based on their likelihood and impact, allowing teams to prioritize which risks need the most attention. Quantitative methods, such as probability and impact matrices, help in evaluating the severity of each risk. After assessing the risks, mitigation strategies are developed and implemented to minimize or eliminate the identified threats.
β
This might include redesigning processes, implementing additional controls, or enhancing monitoring mechanisms. The effectiveness of these strategies is continuously monitored to ensure that the risks are kept under control. By integrating risk analysis into the Six Sigma framework, organizations can not only improve quality and efficiency but also safeguard against potential disruptions, ensuring more robust and resilient processes.
β
β
β
Six Sigma Risk Analysis is crucial because it systematically identifies, assesses, and mitigates risks in business processes, enhancing quality and efficiency. This method reduces defects and errors, leading to improved customer satisfaction and increased profitability.
β
By focusing on data-driven decision-making, Six Sigma ensures that risks are managed proactively, which is essential for maintaining competitive advantage and operational excellence.
β
Six Sigma Risk Analysis improves quality by systematically identifying and eliminating defects and errors in processes. This approach uses statistical tools to analyze data and pinpoint areas of improvement. By addressing the root causes of defects, organizations can produce higher-quality products and services.
β
This not only meets but often exceeds customer expectations, leading to increased satisfaction and loyalty. Enhanced quality also reduces the need for rework, saving time and resources, and ensuring that the final output is consistent and reliable.
β
Implementing Six Sigma Risk Analysis streamlines processes, reducing variability and eliminating inefficiencies. By analyzing data and identifying bottlenecks, organizations can optimize their operations to work more smoothly and effectively.
β
This results in faster cycle times and increased productivity. Efficient processes mean fewer delays and lower costs, as resources are used more effectively. Ultimately, increased efficiency enhances overall business performance, allowing companies to respond more quickly to market demands and opportunities.
β
Six Sigma Risk Analysis enhances customer satisfaction by ensuring consistent delivery of high-quality products and services. By reducing defects and improving process reliability, organizations can meet customer expectations more consistently.
β
Satisfied customers are more likely to become repeat buyers and recommend the company to others. This not only boosts sales but also builds a strong reputation in the market. Enhanced customer satisfaction is crucial for long-term business success and maintaining a loyal customer base.
β
Six Sigma Risk Analysis emphasizes data-driven decision-making, minimizing reliance on intuition and guesswork. By using statistical data and analytical tools, organizations can make informed decisions that are based on objective evidence.
β
This approach leads to more accurate and reliable outcomes, as decisions are grounded in real data rather than assumptions. Data-driven decision-making enhances strategic planning, resource allocation, and problem-solving, contributing to better overall business performance.
β
Proactive risk management is a core benefit of Six Sigma Risk Analysis. By identifying potential risks early in the process, organizations can develop and implement mitigation strategies before issues escalate.
β
This proactive approach prevents disruptions, reduces the likelihood of project delays, and ensures smoother operations. Effective risk management also helps maintain compliance with regulatory requirements and industry standards, safeguarding the organizationβs reputation and operational integrity.
β
Six Sigma Risk Analysis helps reduce costs by minimizing defects, errors, and inefficiencies in processes. By streamlining operations and eliminating waste, organizations can lower production costs and improve profitability.
β
Cost savings are achieved through reduced rework, less scrap, and more efficient use of resources. These savings can be reinvested into the business for further improvements or passed on to customers in the form of competitive pricing, enhancing the companyβs market position.
β
Implementing Six Sigma Risk Analysis provides organizations with a competitive advantage by consistently delivering superior products and services. Higher quality and increased efficiency set companies apart from their competitors, attracting more customers and increasing market share.
β
A reputation for excellence and reliability fosters customer loyalty and trust. Additionally, the continuous improvement culture promoted by Six Sigma ensures that organizations remain agile and responsive to market changes, maintaining their edge over competitors.
β
Choosing the right Six Sigma tool for risk analysis is crucial for effectively identifying, assessing, and mitigating risks in your processes. The selection depends on various factors, including the specific needs of your project, the complexity of your processes, and the nature of the risks involved.
β
Understanding the strengths and limitations of different Six Sigma tools can help you make an informed decision. This guide will cover key considerations to help you choose the most appropriate tool for your risk analysis needs.
β
Begin by clearly defining the specific needs and objectives of your project. Determine the type and level of risks involved, the complexity of your processes, and the desired outcomes. Understanding these requirements will help you narrow down the list of suitable Six Sigma tools.
β
For instance, some projects may need comprehensive statistical analysis, while others might benefit more from simpler visual tools. Aligning the tool selection with your projectβs unique demands ensures more effective risk management. This foundational step sets the stage for selecting the most appropriate tools.
β
Evaluate the capabilities of different Six Sigma tools to ensure they meet your project's requirements. Consider whether the tools can handle the type of data you have, perform the necessary analyses, and generate actionable insights.
β
Tools like Failure Modes and Effects Analysis (FMEA) are excellent for identifying and prioritizing potential failures, while Control Charts are useful for monitoring process stability. By matching tool capabilities with project needs, you ensure that the tools you choose will be effective in addressing specific risk analysis requirements.
β
The ease of use of a Six Sigma tool is crucial for its successful implementation. Assess how intuitive and user-friendly the tool is, especially for team members who may not have extensive Six Sigma training. Tools that are easy to learn and use can improve productivity and reduce the learning curve.
β
Look for features like clear interfaces, helpful tutorials, and support resources. A user-friendly tool promotes broader adoption and more effective risk management across the organization, ensuring that team members can effectively utilize the tool without extensive training.
β
Scalability is an important factor when choosing a Six Sigma tool for risk analysis. Ensure the tool can scale with your project and organizationβs needs, accommodating increasing data volumes and complexity over time.
β
A scalable tool can adapt to larger projects or more sophisticated analyses as your business grows. This flexibility ensures that your risk analysis processes remain robust and effective, regardless of changes in project scope or organizational size. A scalable tool is an investment in your companyβs future growth and adaptability.
β
Verify whether the Six Sigma tool can integrate seamlessly with your existing systems and software. Integration capabilities are important for ensuring smooth data flow and efficient collaboration across different departments.
β
A tool that works well with your current infrastructure can streamline processes, reduce redundancies, and enhance overall efficiency. Look for compatibility with project management tools, data analytics software, and other relevant systems to maximize the benefits of your chosen Six Sigma tool. Proper integration enhances the toolβs utility and effectiveness in your operations.
β
Consider the cost and resource requirements of implementing and maintaining the Six Sigma tool. Assess whether the investment aligns with your budget and the value it brings to your risk analysis efforts.
β
Take into account not only the initial purchase cost but also any ongoing expenses, such as training, support, and software updates. Balancing cost-effectiveness with functionality ensures that you choose a tool that delivers a good return on investment. A thorough cost-benefit analysis helps in making a financially sound decision.
β
Consulting with Six Sigma experts or experienced practitioners can provide valuable insights into selecting the right tool for your needs. They can offer recommendations based on their knowledge and experience, helping you navigate the various options available.
β
Expert guidance can also assist in tailoring the tool to your specific project requirements, ensuring more effective risk analysis and management. Leveraging expert advice enhances your decision-making process and helps you implement the best Six Sigma practices. This collaborative approach enriches the tool selection and implementation process.
β
Several robust Six Sigma tools and frameworks are widely used for effective risk analysis in organizational processes. Each tool offers unique strengths tailored to different aspects of risk management, from identifying potential failures to implementing mitigation strategies.
β
Understanding these tools and their applications can significantly enhance your ability to manage risks and improve process outcomes. This guide explores some of the best Six Sigma tools and frameworks renowned for their effectiveness in mitigating risks and ensuring high-quality, efficient operations.
β
Failure Modes and Effects Analysis (FMEA) is a structured approach used to identify and analyze potential failure modes within a system, process, or product. It assesses the impact of these failures based on their severity, likelihood of occurrence, and detectability.
β
FMEA helps organizations prioritize risks and implement effective mitigation strategies to prevent failures from occurring. By identifying potential issues early, FMEA enhances the reliability, safety, and quality of processes and products, ensuring that risks are managed proactively and systematically.
β
β
Control Charts are graphical tools used to monitor process variation over time. They help detect deviations and trends that indicate potential problems, allowing for timely corrective actions.
β
Control Charts are essential for establishing process stability and maintaining consistent quality by ensuring that processes remain within defined control limits. By visualizing data in real-time, organizations can identify areas for improvement and make data-driven decisions to enhance process performance and product quality.
β
β
Root Cause Analysis (RCA) is a method used to identify the underlying causes of problems and process issues. By focusing on the root causes rather than symptoms, RCA helps organizations implement effective corrective actions to prevent recurrence.
β
This approach enhances process efficiency and reliability, promotes continuous improvement, and reduces the likelihood of future failures. RCA is critical for maintaining long-term process stability and addressing issues at their source.
β
β
Design of Experiments (DOE) is a systematic approach to testing process factors and their interactions to optimize outcomes. By identifying critical variables and their effects, DOE helps reduce variability, strengthen process robustness, and enhance product quality.
β
This method supports data-driven process improvements and allows organizations to make informed decisions about optimizing parameters, ultimately leading to more reliable and efficient processes.
β
β
Risk Priority Number (RPN) is a numerical scoring system used in FMEA to quantify risks based on severity, occurrence, and detectability. RPN helps prioritize risks, allowing organizations to focus on high-impact areas and allocate resources effectively.
β
By assigning scores to different risks, RPN enhances risk management strategies, ensuring that critical risks are addressed proactively and systematically. This approach supports continuous monitoring and updating of risk assessments.
β
β
Statistical Process Control (SPC) uses statistical methods to monitor and control processes, ensuring stability and quality. SPC involves real-time tracking of process performance and early detection of deviations using statistical tools.
β
By maintaining consistency and predictability, SPC supports proactive quality control measures and continuous process improvement. This approach helps organizations identify trends, reduce variability, and enhance overall process performance.
β
β
Lean Six Sigma combines Lean principles for efficiency with Six Sigma methodologies for quality improvement. This integrated approach focuses on eliminating waste, reducing process variability, and enhancing overall process efficiency and customer satisfaction.
β
By streamlining processes and promoting a culture of continuous improvement, Lean Six Sigma supports sustainable business growth and operational excellence.
β
β
β
β
Enterprise Risk Management (ERM) encompasses a comprehensive approach to identifying, assessing, and managing risks that affect an organization's ability to achieve its objectives.It integrates risk management practices across all levels of the organization, aligning strategies with risk tolerance and ensuring resilience in the face of uncertainties.
β
The eight key components of ERM provide a structured framework for organizations to proactively address risks, optimize opportunities, and enhance decision-making processes. These components collectively foster a culture of risk awareness and preparedness, crucial for sustainable growth and operational success amidst evolving challenges and competitive landscapes.
β
The internal environment establishes the foundation for risk management within an organization. It includes the organizational culture, governance structure, and risk appetite. A robust internal environment fosters risk awareness, accountability, and ethical behavior across all levels of the organization.
β
By promoting these values, organizations create a proactive approach to identifying and managing risks. This environment ensures that employees are aware of their roles in risk management and are motivated to act responsibly in the face of potential threats and opportunities.
β
Objective setting involves defining the goals and targets an organization aims to achieve. Effective Enterprise Risk Management (ERM) ensures that risk management strategies are aligned with these objectives. This alignment helps in identifying and managing risks that could impact the achievement of organizational goals and performance metrics.
β
By integrating risk considerations into the objective-setting process, organizations can better anticipate challenges and opportunities, ensuring that their strategic direction remains resilient and adaptive to changing conditions.
β
Event identification is the process of recognizing potential events that could affect the achievement of organizational objectives. These events can be either risks or opportunities that need to be assessed and managed appropriately.
β
Identifying these events early allows organizations to prepare for potential disruptions and capitalize on favorable circumstances. By systematically scanning the internal and external environments for potential events, organizations can enhance their ability to respond effectively to unforeseen changes and maintain their strategic focus.
β
Risk assessment involves evaluating the likelihood and impact of identified risks on the organization. This step helps prioritize risks based on their significance, allowing resources to be allocated efficiently for mitigation.
β
By assessing risks, organizations can determine which risks pose the greatest threats and require immediate attention. This process involves analyzing both qualitative and quantitative data to provide a comprehensive understanding of the potential impact of risks, supporting informed decision-making and effective risk management strategies.
β
Once risks are assessed, organizations develop risk response strategies to address them. These strategies can include avoiding, reducing, sharing, or accepting risks, depending on their impact and alignment with organizational objectives.
β
Effective risk response ensures that risks are managed in a way that minimizes their negative impact while maximizing potential benefits. By selecting the appropriate response for each risk, organizations can enhance their resilience and maintain their strategic direction in the face of uncertainty.
β
Control activities are the policies, procedures, and practices implemented to mitigate risks and ensure that risk responses are effective. These controls help safeguard assets, optimize operations, and enhance the reliability of financial reporting.
β
By establishing robust control activities, organizations can ensure that risk management strategies are executed as planned and that potential deviations are promptly addressed. Effective control activities provide a framework for maintaining operational efficiency and achieving organizational objectives.
β
Effective ERM requires timely and relevant information to support decision-making processes. Communication ensures that risk information is shared across the organization, fostering transparency and accountability in risk management.
β
By providing accurate and up-to-date information, organizations can make informed decisions and respond quickly to emerging risks. Clear communication channels facilitate the flow of information between different levels of the organization, ensuring that all stakeholders are aware of their roles and responsibilities in managing risks.
β
Monitoring involves ongoing evaluation of the effectiveness of ERM processes. It ensures that risk responses are implemented as planned, risks are managed within acceptable levels, and changes in the risk environment are promptly addressed.
β
Continuous monitoring helps organizations adapt to new challenges and opportunities, maintaining the effectiveness of their risk management strategies. By regularly reviewing and updating ERM processes, organizations can ensure that they remain resilient and capable of achieving their long-term objectives.
β
These eight components provide a structured approach to integrating risk management into organizational processes, promoting resilience, and enhancing long-term value creation. By addressing each component comprehensively, organizations can mitigate threats, capitalize on opportunities, and achieve sustainable growth.
β
Lean Six Sigma combines the principles of Lean manufacturing, focused on efficiency and waste reduction, with Six Sigma methodologies, aimed at quality improvement and defect reduction.
β
This integrated approach emphasizes identifying and eliminating waste, optimizing processes, and reducing variation to enhance overall operational efficiency and customer satisfaction. Lean Six Sigma uses data-driven techniques and continuous improvement strategies to streamline operations, improve productivity, and deliver high-quality products or services consistently.
β
By integrating these two powerful methodologies, organizations can achieve significant cost savings, operational excellence, and sustainable competitive advantage in today's dynamic business environment.
β
Customer focus in Lean Six Sigma entails understanding and prioritizing customer requirements throughout all organizational processes. By aligning operations with customer needs and expectations, organizations can enhance customer satisfaction and loyalty.
β
This involves gathering feedback, analyzing customer data, and ensuring that product or service features align with market demands. Customer-focused initiatives aim to deliver value and quality that directly meet customer expectations, thereby driving competitive advantage and sustaining long-term relationships.
β
Data-driven decision-making in Lean Six Sigma involves using statistical tools and analysis to evaluate processes objectively. By collecting and analyzing relevant data, organizations can identify trends, patterns, and root causes of variability or defects.
β
This empirical approach enables informed decision-making, where adjustments and improvements are based on concrete evidence rather than assumptions. Statistical methods such as hypothesis testing, control charts, and regression analysis provide insights into process performance, guiding initiatives to optimize efficiency, reduce waste, and enhance overall quality.
β
Continuous improvement is at the core of Lean Six Sigma, promoting a culture where every employee actively seeks opportunities for enhancement. This involves systematically identifying inefficiencies, addressing root causes of problems, and implementing sustainable solutions.
β
Through practices like Kaizen events, PDCA (Plan-Do-Check-Act) cycles, and Lean tools such as 5S (Sort, Set in order, Shine, Standardize, Sustain), organizations continually refine processes to achieve higher levels of performance and reliability. Continuous improvement not only drives operational excellence but also cultivates a proactive mindset focused on innovation and responsiveness to changing market dynamics.
β
Cross-functional teamwork in Lean Six Sigma emphasizes collaboration across different departments and functions within an organization. By breaking down silos and fostering interdepartmental communication, teams can share knowledge, leverage diverse perspectives, and collectively work towards achieving shared objectives.
β
This collaborative approach enhances problem-solving capabilities, facilitates faster decision-making, and promotes a holistic understanding of organizational processes. Cross-functional teams often lead improvement projects, pooling together expertise from various disciplines to implement comprehensive solutions that address multifaceted challenges and optimize overall business outcomes.
β
Six Sigma operates on five fundamental principles that form the core of its methodology for process improvement and quality management. These principles are essential for organizations aiming to achieve high levels of performance, customer satisfaction, and sustainable growth through structured and data-driven approaches.
β
Each principle contributes uniquely to the overall goal of reducing defects, minimizing variation, and optimizing processes to deliver consistent value to customers and stakeholders. Understanding and applying these principles effectively enable organizations to enhance operational efficiency, drive continuous improvement, and maintain competitive advantage in dynamic market environments.
β
Customer focus is integral to Six Sigma, ensuring that organizational processes are aligned with customer needs and expectations. By understanding customer requirements and preferences, organizations can deliver products and services that consistently meet or exceed customer satisfaction levels.
β
This principle drives organizations to prioritize customer feedback, integrate customer-centric metrics into process evaluations, and continuously improve offerings to enhance customer experience and loyalty.
β
Six Sigma relies heavily on statistical analysis and data-driven approaches to identify, measure, and analyze process performance. This principle emphasizes the collection and analysis of accurate data to make informed decisions based on facts rather than assumptions.
β
Statistical tools such as hypothesis testing, control charts, and regression analysis enable organizations to pinpoint root causes of variation and defects, guiding effective problem-solving and improvement efforts.
β
Process improvement is central to Six Sigma, focusing on systematically enhancing processes to achieve higher levels of efficiency and quality. This principle involves identifying areas of waste, inefficiency, or defects within processes, applying structured methodologies like DMAIC (Define, Measure, Analyze, Improve, Control) or DMADV (Define, Measure, Analyze, Design, Verify) to streamline workflows, reduce cycle times, and optimize resource utilization.
β
Continuous process improvement ensures that organizations can adapt to changing market conditions and customer requirements while maintaining operational excellence.
β
Six Sigma promotes proactive management practices aimed at preventing defects and errors before they impact product quality or customer satisfaction. This principle encourages organizations to implement robust quality control measures, standardize processes, and establish preventive maintenance schedules to mitigate risks and ensure consistent performance.
β
By anticipating potential issues and implementing preventive actions, organizations can minimize disruptions, enhance reliability, and sustain high levels of product and service quality over time.
β
The pursuit of perfection is a core tenet of Six Sigma, advocating for a culture of continuous improvement and excellence across all organizational functions. This principle challenges teams to strive for higher standards, innovate processes, and embrace change to drive ongoing growth and development.
β
By fostering a culture that values learning, innovation, and achieving measurable results, organizations can sustain competitive advantage, adapt to market dynamics, and meet evolving customer expectations effectively.
β
Six Sigma provides two core methodologies: DMAIC (Define, Measure, Analyze, Improve, Control) and DMADV (Define, Measure, Analyze, Design, Verify). These frameworks are tailored for enhancing existing processes (DMAIC) and developing new processes or products (DMADV).
β
DMAIC focuses on eliminating defects and optimizing performance through data-driven analysis and iterative improvements. In contrast, DMADV emphasizes proactive design and validation to ensure new solutions meet customer needs and operational goals from inception. Both methodologies integrate rigorous problem-solving techniques to achieve measurable enhancements and sustainable results in quality management and operational efficiency.
β
DMAIC (Define, Measure, Analyze, Improve, Control) is a structured approach used in Six Sigma for improving existing processes. It begins with defining the problem and project goals, ensuring clarity on customer requirements and measurable objectives. The measure phase involves quantifying process performance metrics and collecting data to establish a baseline for analysis.Β
β
Analysis employs statistical tools to identify root causes of defects or inefficiencies. In the improve phase, solutions are developed and implemented to optimize process performance and meet customer needs. Control mechanisms are then established to monitor ongoing performance, sustain improvements, and prevent regression. DMAIC's iterative nature enables continuous refinement, achieving significant enhancements in quality, efficiency, and customer satisfaction.
β
DMADV (Define, Measure, Analyze, Design, Verify) is utilized for designing new processes or products that are robust and meet customer needs from inception. It begins with defining project goals based on comprehensive customer requirements and market expectations. Measurement involves quantifying critical-to-quality factors and setting performance metrics for the new process or product. Analysis focuses on understanding and prioritizing customer needs, translating them into specific design requirements.Β
β
Designing entails developing a detailed plan that integrates customer specifications, ensuring reliability and efficiency. Verification involves rigorous testing, simulation, and pilot runs to validate the design meets performance standards and customer expectations. DMADV emphasizes proactive planning and design, delivering innovative solutions aligned with strategic business objectives.
β
β
β
Six Sigma facilitates business transformation through a systematic approach aimed at improving operational efficiency and quality management. It employs rigorous methodologies like DMAIC (Define, Measure, Analyze, Improve, Control) and DMADV (Define, Measure, Analyze, Design, Verify) to address existing process inefficiencies and design new solutions aligned with customer needs.
β
By integrating data-driven analysis, statistical tools, and continuous improvement principles, Six Sigma enhances organizational performance, reduces defects, and optimizes processes across all levels. This structured approach fosters a culture of continuous learning and innovation, driving sustainable growth and competitive advantage in dynamic market environments.
β
The Define phase in Six Sigma initiates the project by clearly defining the problem, project goals, and customer requirements. This step sets the scope and objectives of the improvement or design effort. It involves gathering information from stakeholders to understand their expectations and establish measurable metrics for success.
β
A well-defined project charter is created to outline the project's purpose, scope, stakeholders, timeline, and resources. Effective communication and alignment of goals ensure that all team members and stakeholders have a clear understanding of the project's objectives and desired outcomes before proceeding to the next phases.
β
In the Measure phase, the focus shifts to quantifying the current state of the process using data-driven methods. Key performance metrics (KPIs) are identified and measured to establish a baseline against which improvements can be evaluated. Data collection techniques such as process mapping, data sampling, and statistical analysis are employed to gather accurate and relevant data.
β
This phase aims to provide a factual understanding of process performance and variability, identifying areas that contribute to defects or inefficiencies. The measured data serves as a basis for subsequent analysis and decision-making, guiding the project towards meaningful improvements.
β
During the Analyze phase, statistical tools and techniques are utilized to analyze the collected data in depth. The primary objective is to identify root causes of problems, defects, or variations within the process. Techniques such as Pareto analysis, root cause analysis (RCA), hypothesis testing, and correlation analysis are employed to uncover patterns, trends, and relationships that impact process outcomes.
β
By pinpointing the underlying factors contributing to issues, teams can prioritize improvement efforts effectively. Data analysis not only validates assumptions but also provides insights into where interventions are most needed to achieve significant process enhancements.
β
In the Improve phase, solutions are developed and implemented based on the findings from the analysis phase. Teams brainstorm and evaluate potential solutions, focusing on addressing root causes identified earlier. Quality tools like brainstorming sessions, design of experiments (DOE), and pilot tests are utilized to test proposed solutions on a small scale before full implementation.
β
Continuous feedback and iteration refine solutions to ensure they effectively meet project goals and customer requirements. The goal is to optimize processes, reduce defects, enhance efficiency, and ultimately deliver improved outcomes that align with organizational objectives.
β
The Control phase aims to sustain the improvements achieved throughout the project. Control measures and monitoring systems are established to ensure that process performance remains stable and within acceptable limits. Key activities include developing control plans, implementing standard operating procedures (SOPs), training personnel, and setting up monitoring mechanisms such as statistical process control (SPC) charts.
β
Continuous monitoring and measurement of KPIs allow teams to detect deviations early and take corrective actions promptly. By embedding controls into the process, organizations can prevent regression, maintain gains, and sustain long-term improvements in quality, efficiency, and customer satisfaction.
β
Six Sigma techniques encompass a variety of tools and methodologies designed to improve processes, reduce defects, and enhance overall quality within organizations. These techniques are rooted in data-driven analysis and systematic problem-solving approaches aimed at achieving measurable and sustainable results.
β
From statistical tools like Pareto analysis and regression analysis to process mapping and control charts, Six Sigma techniques empower teams to identify root causes of issues, optimize processes, and implement effective solutions. By integrating these methodologies, organizations can streamline operations, enhance customer satisfaction, and maintain competitive advantage in dynamic business environments.
β
Pareto Analysis is a powerful tool derived from the Pareto Principle (80/20 rule), which states that roughly 80% of effects come from 20% of causes. This technique helps teams prioritize efforts by identifying and focusing on the most significant factors contributing to problems or defects.
β
By analyzing data and categorizing issues based on their frequency or impact, Pareto charts visually represent the cumulative impact of different factors. This approach guides organizations to allocate resources efficiently and address the vital few causes that yield the most significant improvements in quality and efficiency.
β
The Cause and Effect Diagram, also known as the Fishbone Diagram due to its fishbone-like structure, is a visual tool used to identify potential causes contributing to a specific problem or effect. It categorizes potential causes into major categories such as people, process, equipment, materials, environment, and management (the 6Ms).
β
By organizing brainstormed ideas and root causes in a structured manner, teams can systematically investigate and address the underlying reasons for issues. This facilitates targeted improvements and solutions, enhancing process understanding and problem-solving effectiveness.
β
DMAIC is a structured problem-solving methodology used for improving existing processes within organizations. Each phaseβDefine, Measure, Analyze, Improve, and Controlβprovides a systematic approach to identify, analyze, and eliminate variations or defects in processes. DMAIC emphasizes data-driven decision-making, statistical analysis, and continuous improvement to achieve measurable and sustainable results.
β
It enables teams to define project goals clearly, measure process performance accurately, analyze data to identify root causes comprehensively, implement and verify improvements effectively, and establish controls to sustain gains over time.
β
Statistical Process Control (SPC) involves monitoring and controlling process variability using statistical methods. It utilizes control charts to visualize process performance over time, distinguishing between common cause variation (inherent to the process) and special cause variation (resulting from external factors or process changes).
β
SPC helps organizations maintain process stability, predictability, and consistency by providing early detection of deviations and enabling timely corrective actions. By leveraging statistical tools and control charts, SPC empowers teams to proactively manage processes and drive continuous improvement in quality and efficiency.
β
Design of Experiments (DOE) is a systematic approach used to identify and optimize critical factors that affect process or product performance. DOE allows teams to conduct controlled experiments by manipulating variables and observing their effects on outcomes.
β
By systematically varying inputs and analyzing their impact on outputs, organizations can uncover the most influential factors, optimize processes, and achieve robust designs that meet desired specifications. DOE facilitates informed decision-making, reduces variability, and enhances process efficiency through empirical testing and data-driven insights.
β
Control Charts are essential tools in Six Sigma for monitoring process performance and identifying trends or patterns over time. They plot data points against established control limits to distinguish between common cause variation (normal process variation) and special cause variation (unusual events or changes).
β
By providing a visual representation of process stability, control charts enable teams to make informed decisions and take proactive measures to maintain consistent quality. Continuous monitoring with control charts supports ongoing improvement efforts by detecting deviations early and facilitating timely corrective actions to optimize process performance.
β
Root Cause Analysis (RCA) is a systematic approach used to identify the fundamental reasons behind problems or defects within processes. It involves probing deeper into the layers of causes using techniques such as the 5 Whys (repeatedly asking "why" to uncover root causes) and Cause and Effect diagrams (Fishbone diagrams).
β
By addressing root causes rather than symptoms, RCA helps organizations implement targeted corrective actions that prevent recurrence and improve overall process reliability. This method fosters a culture of continuous improvement and proactive problem-solving, enhancing operational efficiency and customer satisfaction.
β
Kaizen, translating to "continuous improvement" in Japanese, embodies a philosophy and methodology focused on making incremental changes to enhance processes, products, or services over time. It advocates for a culture of continuous learning, employee involvement, and small, iterative improvements to achieve significant long-term results.
β
Kaizen techniques include brainstorming sessions, Gemba walks (on-site observations to understand processes), and employee suggestion systems. By nurturing a Kaizen mindset, organizations empower employees to identify opportunities for improvement, drive efficiency gains, and adapt swiftly to evolving customer needs and market dynamics.
β
β
β
Six Sigma encompasses a range of powerful tools and methodologies designed to enhance process quality, reduce defects, and drive organizational improvement. These tools are rooted in data-driven analysis and systematic problem-solving approaches, aimed at achieving measurable and sustainable results.
β
From statistical techniques like Pareto Analysis and Control Charts to structured methodologies such as DMAIC and DMADV, Six Sigma tools empower teams to identify root causes of issues, optimize processes, and implement effective solutions.
β
By leveraging these tools, organizations can enhance efficiency, minimize variability, and consistently deliver products and services that meet or exceed customer expectations.
β
β
Six Sigma uses a hierarchy of certification levels to denote expertise and proficiency in implementing its methodologies within organizations. These levels signify varying degrees of mastery and leadership in driving quality improvements and process optimizations.
β
From foundational understanding at the Yellow Belt level to advanced statistical analysis and project management skills at the Black Belt and Master Black Belt levels, each certification equips professionals with specific tools and techniques.
β
Six Sigma levels empower individuals to lead projects, mentor teams, and drive organizational change towards achieving excellence in quality, efficiency, and customer satisfaction.
β
White Belts are entry-level participants in Six Sigma initiatives. They have a basic understanding of Six Sigma concepts and terminologies but typically do not lead projects. Instead, White Belts support improvement efforts within their teams or departments by participating in meetings, workshops, and training sessions.
β
They may assist with data collection, basic analysis, and implementation of improvement solutions under the guidance of higher-level belts. White Belts play a crucial role in familiarizing themselves with Six Sigma principles and preparing to advance to higher levels of certification.
β
Yellow Belts have foundational knowledge of Six Sigma methodologies. They understand basic tools and techniques used in process improvement projects. Yellow Belts typically work as team members on improvement projects, assisting in data collection, process mapping, and analysis. They contribute to identifying root causes of problems and implementing solutions within their scope of work.
β
Yellow Belts support Green Belts and Black Belts by providing data and participating actively in improvement efforts. Their role helps build practical experience and prepares them for more significant responsibilities in process improvement.
β
Green Belts possess intermediate-level proficiency in Six Sigma. They lead smaller-scale improvement projects or assist Black Belts in larger projects. Green Belts are skilled in statistical analysis, process mapping, and problem-solving techniques.
β
They apply Six Sigma tools such as DMAIC (Define, Measure, Analyze, Improve, Control) to identify areas for improvement, measure performance metrics, analyze data for root causes, implement solutions, and establish control mechanisms. Green Belts play a pivotal role in driving process enhancements, reducing defects, and improving efficiency within their designated projects or departments.
β
Black Belts are experts in Six Sigma methodologies and lead significant improvement projects within organizations. They possess advanced knowledge of statistical analysis, project management, and change leadership. Black Belts mentor Green Belts and work closely with stakeholders to define project goals, scope, and deliverables.
β
They conduct in-depth data analysis, identify critical process factors affecting quality and performance, and implement robust solutions to achieve measurable results. Black Belts ensure projects align with organizational objectives, sustain improvements over time, and drive cultural change towards a continuous improvement mindset.
β
Master Black Belts are seasoned Six Sigma leaders with extensive experience and expertise in driving organizational transformation through Six Sigma methodologies. They oversee multiple projects across departments or the entire organization, providing strategic guidance and mentorship to Black Belts and Green Belts.
β
Master Black Belts play a crucial role in setting Six Sigma standards, developing training programs, and aligning improvement efforts with business strategies. They facilitate collaboration between different teams, monitor overall progress, and champion continuous improvement initiatives to achieve significant quality and efficiency improvements organization-wide.
β
Each Six Sigma level represents a progression in knowledge, skills, and responsibilities, contributing to the organization's overall success in achieving operational excellence and customer satisfaction through systematic process improvement.
β
β
β
Six Sigma certifications open doors to diverse career opportunities across industries, emphasizing roles in quality management, process improvement, and operational excellence.
β
Professionals certified at different levelsβWhite Belt, Yellow Belt, Green Belt, Black Belt, and Master Black Beltβcan pursue careers as quality engineers, project managers, process improvement specialists, and operations managers. Salaries vary significantly based on certification level, industry, and experience.
β
Typically, higher-level certifications command higher salaries, reflecting the expertise and leadership required to drive significant improvements in organizational efficiency and quality. Career growth in Six Sigma often includes roles in management and executive leadership, influencing strategic decision-making and business performance.
β
β
Six Sigma stands as a robust methodology that drives organizational excellence through structured processes, data-driven decision-making, and continuous improvement initiatives. By focusing on minimizing variation and defects, Six Sigma enables organizations to enhance efficiency, optimize performance, and consistently deliver high-quality products and services.
β
It fosters a culture of rigorous problem-solving and empowers teams at all levels to contribute to process improvement efforts. Ultimately, Six Sigma not only aims to meet customer needs effectively but also to sustain long-term business success by aligning operational practices with strategic goals. Adopting Six Sigma principles equips organizations with the tools and methodologies necessary to achieve and maintain competitive advantage in today's global marketplace.
Copy and paste below code to page Head section
Six Sigma is a data-driven methodology used to improve processes by identifying and eliminating defects. It aims to achieve near-perfect quality by reducing variability and improving efficiency across all areas of operation.
The levels of Six Sigma certification include White Belt, Yellow Belt, Green Belt, Black Belt, and Master Black Belt. Each level signifies a different degree of expertise and responsibility in Six Sigma methodologies.
Six Sigma improves process efficiency by using statistical tools to analyze data, identify root causes of defects, and implement solutions. This approach reduces variability and enhances overall process performance.
A Six Sigma Green Belt supports process improvement projects by analyzing data and implementing solutions. They work under the guidance of Black Belts, focusing on reducing defects and improving efficiency.
Six Sigma is implemented through a structured approach called DMAIC (Define, Measure, Analyze, Improve, Control). This process involves defining the problem, measuring current performance, analyzing data, implementing improvements, and controlling the new process to ensure sustained results.
Benefits of Six Sigma certification include improved career prospects, increased earning potential, enhanced problem-solving skills, and the ability to contribute to organizational efficiency and quality improvements.