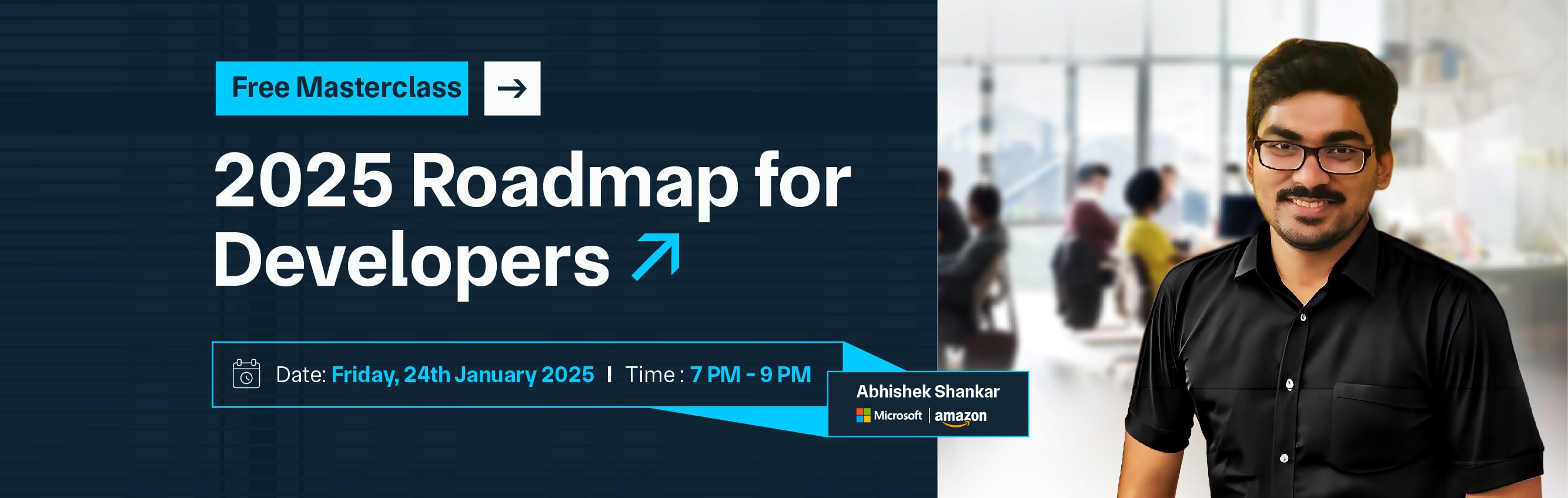
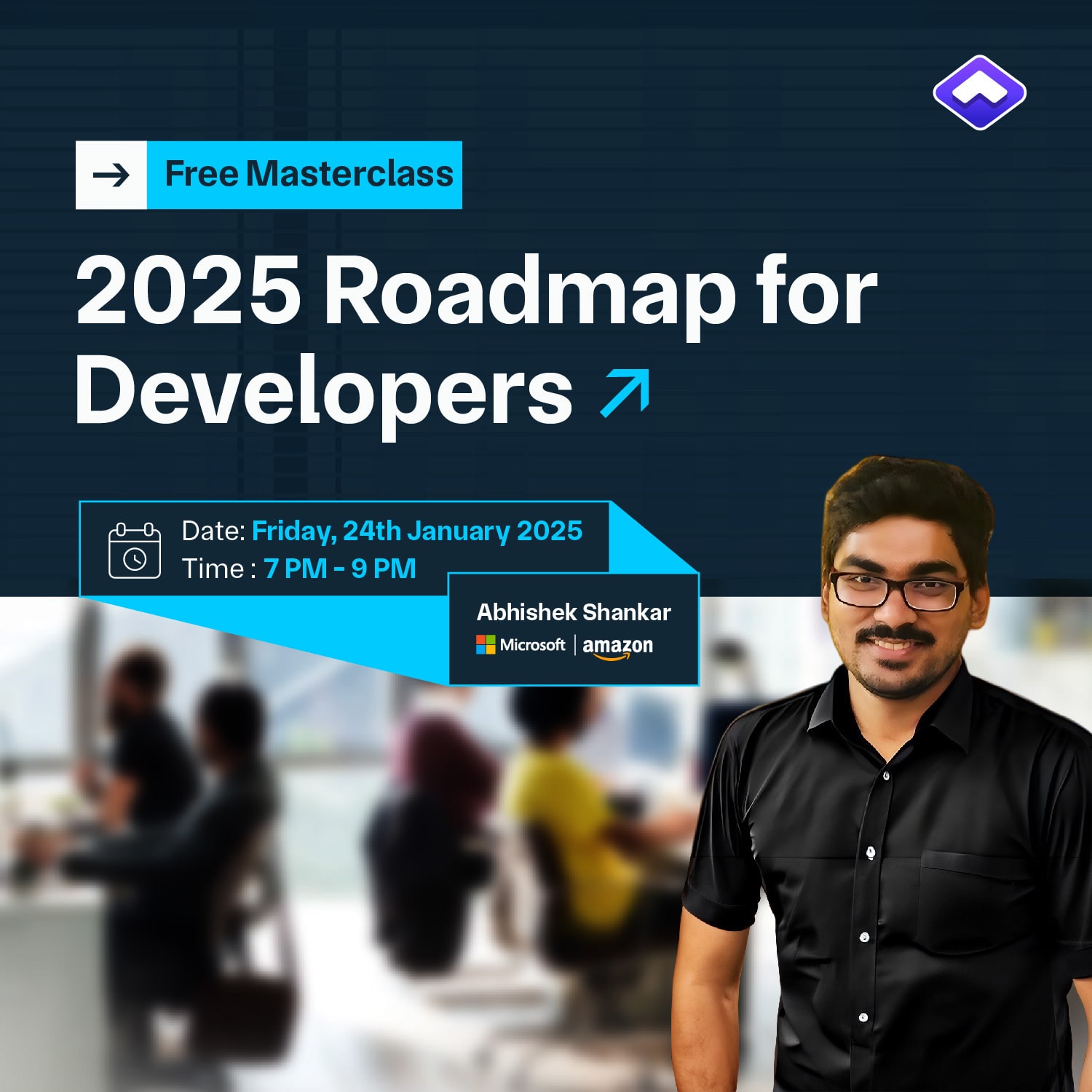
Six Sigma is a structured, data-driven approach aimed at improving processes by minimizing errors and enhancing quality. Its focus on measurable outcomes makes it invaluable in analyzing requirements for projects or products. Through Six Sigma techniques, organizations can identify inefficiencies, understand customer needs, and ensure that the requirements align with business goals. The objective is not only to meet specifications but to exceed expectations by reducing variability and improving consistency.
The Six Sigma approach leverages a range of tools, such as DMAIC (Define, Measure, Analyze, Improve, Control), to assess requirements accurately. During the “Define” phase, teams identify core objectives and clarify customer needs, while the “Measure” and “Analyze” stages provide a comprehensive view of current performance against those needs. By identifying root causes and quantifying requirements, organizations can focus on the most impactful improvements, enhancing process reliability and customer satisfaction.
When applied to requirements analysis, Six Sigma helps prevent project scope creep, reduce development time, and cut unnecessary costs. The framework ensures that every requirement aligns with the quality standards essential for successful project outcomes. Through statistical analysis and continuous improvement, Six Sigma enables teams to make well-informed decisions and achieve results that add real value to the business.
Six Sigma is a methodology focused on improving processes by reducing variation and eliminating defects to achieve high levels of quality and efficiency. Originating in manufacturing, Six Sigma has since expanded to various industries as it provides a systematic, data-driven approach to problem-solving. The central goal of Six Sigma is to limit errors to fewer than 3.4 defects per million opportunities, ensuring near-perfect process consistency. By applying statistical tools, Six Sigma helps organizations identify the root causes of problems, make measurable improvements, and enhance customer satisfaction.
The Six Sigma approach typically follows the DMAIC process: Define, Measure, Analyze, Improve, and Control. This framework allows teams to clearly define goals, quantify existing performance, and implement sustainable improvements. Organizations that adopt Six Sigma benefit from lower costs, higher efficiency, and greater product or service quality. Six Sigma’s emphasis on data and structured problem-solving makes it a powerful tool for companies aiming to achieve operational excellence.
Lean Six Sigma combines the principles of Lean methodology with Six Sigma, creating a powerful approach that focuses on both speed and quality. Lean aims to streamline operations by eliminating waste and optimizing workflows, while Six Sigma reduces variability and improves precision. Together, Lean Six Sigma empowers organizations to deliver high-quality results more efficiently by focusing on continuous improvement and waste reduction. This hybrid approach helps companies minimize delays, reduce costs, and provide more value to customers.
By integrating Lean and Six Sigma tools, Lean Six Sigma addresses inefficiencies and inconsistencies holistically, using methods like value stream mapping, root cause analysis, and process flow improvement. Organizations that use Lean Six Sigma benefit from faster response times, improved resource utilization, and a stronger focus on customer needs. The combined methodology is especially useful in industries where time and quality are critical, ensuring that processes are both optimized and aligned with business objectives.
Six Sigma Risk Analysis is a method within the Six Sigma framework used to identify, assess, and mitigate risks that could impact the quality and efficiency of a process. This analysis helps organizations recognize potential points of failure early in the project lifecycle, allowing for preventive action to reduce defects and improve outcomes. By applying statistical and data-driven techniques, Six Sigma Risk Analysis evaluates the likelihood and impact of risks, focusing on those that could significantly affect quality. This enables teams to prioritize high-risk areas and allocate resources effectively to maintain process stability and meet customer expectations.
In Six Sigma Risk Analysis, tools like Failure Modes and Effects Analysis (FMEA) and risk matrices are often used to categorize risks based on severity and probability. These tools provide a structured approach to documenting potential failures and assessing the consequences associated with each one. Through proactive risk management, Six Sigma Risk Analysis helps organizations minimize variability and ensure that processes remain within quality standards, ultimately fostering more consistent performance and reducing costly disruptions. This approach empowers teams to make informed decisions that align with both process improvement goals and overall business objectives.
Six Sigma Risk Analysis is essential for organizations aiming to achieve consistent quality and minimize process inefficiencies. By proactively identifying and mitigating risks, Six Sigma Risk Analysis allows teams to anticipate potential issues before they disrupt workflows, resulting in a smoother, more predictable process. This analysis helps businesses reduce costs, improve customer satisfaction, and maintain high standards across operations.
The structured, data-driven approach enables organizations to allocate resources effectively, focus on high-risk areas, and make strategic decisions that align with quality objectives. Ultimately, Six Sigma Risk Analysis not only supports operational excellence but also drives continuous improvement, contributing to a competitive advantage in the marketplace.
The core principles of Six Sigma provide a foundation for improving quality, reducing defects, and achieving operational excellence. These principles guide organizations in focusing on customer needs, analyzing processes, and eliminating inefficiencies. By adhering to these principles, companies can build processes that consistently deliver high-quality outcomes while minimizing waste and maximizing efficiency.
Each principle serves as a step toward achieving a data-driven approach to quality management, ensuring that all efforts are aligned with the business’s overall objectives. Understanding and applying these key principles empowers teams to make continuous improvements and drive sustained success across the organization.
The first principle of Six Sigma is setting well-defined, measurable goals that align with the organization’s overall objectives. Six Sigma encourages teams to create specific and achievable goals that reflect both business priorities and quality standards. These objectives should be customer-focused, yet practical, considering both the needs of the organization and the end-user.
Clearly defined goals provide direction and purpose for improvement projects, ensuring that efforts are streamlined and effective. This principle enables teams to track their progress against concrete benchmarks, making it easier to identify successes and areas for improvement. When goals are measurable, it fosters accountability and helps team members remain focused on achieving high-quality outcomes, ultimately driving better performance and greater customer satisfaction.
To improve quality, organizations must fully understand their processes, identifying each step, resource, and factor involved. Six Sigma encourages a detailed mapping of processes to determine where inefficiencies, errors, or bottlenecks may arise. This comprehensive understanding enables teams to pinpoint areas for improvement and control variables that could lead to inconsistent outcomes.
By clarifying each component of the process, teams gain insights into areas that can be optimized for better efficiency and effectiveness. Detailed process understanding also helps identify potential issues that could lead to defects or variability, allowing teams to take proactive steps toward streamlining operations. With a strong grasp of the process flow, teams can ensure a consistent and reliable path to quality production, minimizing waste and reducing unnecessary steps.
A primary goal of Six Sigma is to reduce process variability and eliminate defects to maintain consistent, high-quality results. Six Sigma uses statistical tools to identify and control variations that cause quality issues. By analyzing data on defects and identifying root causes, organizations can systematically remove inconsistencies, resulting in more predictable outcomes. This approach allows for repeatable success and enables teams to achieve near-zero defect rates, which is critical for customer satisfaction and cost reduction.
When process variation is minimized, it also reduces production time and improves the reliability of outputs. Six Sigma provides teams with the tools and methodologies needed to address quality issues at the source, ensuring that products and services meet rigorous standards consistently. The focus on defect elimination supports long-term efficiency and promotes a culture of excellence within the organization.
Six Sigma emphasizes the importance of involving and empowering employees across all levels. Successful Six Sigma projects rely on the insights, expertise, and engagement of team members who directly interact with processes daily. Training and empowering employees fosters a collaborative environment where everyone takes ownership of quality improvement efforts. This active involvement ensures that solutions are practical and sustainable, as employees feel invested in driving change and maintaining high standards.
By cultivating a culture of empowerment, organizations encourage employees to contribute ideas and participate in problem-solving activities. Involving employees also helps identify unique insights and innovative approaches to enhance efficiency. When teams feel empowered, they are more likely to take responsibility for quality outcomes and actively seek out ways to improve.
A data-driven approach is essential to Six Sigma, as it provides objective insights that guide decision-making and improvement efforts. Six Sigma relies on data collection and analysis to validate processes, measure progress, and identify areas for improvement. By basing decisions on empirical evidence rather than assumptions, organizations can make informed adjustments that lead to measurable results.
This principle ensures that improvements are quantifiable, sustainable, and aligned with organizational goals, leading to long-term success. Data-driven methods make it possible to track changes over time, confirm that improvements are effective, and continuously optimize processes. By fostering a data-centric culture, Six Sigma equips teams with the information they need to make precise, impactful decisions and maintain a cycle of continuous improvement.
Choosing the right Six Sigma tool for risk analysis is crucial for effective risk identification, prioritization, and mitigation. Each tool offers unique features suited to different types of projects, data sets, and organizational needs. The goal is to select a tool that aligns with the complexity of the process and the specific risks being addressed. Six Sigma offers several tools, such as Failure Modes and Effects Analysis (FMEA), Root Cause Analysis, and Control Charts, each designed to address different aspects of risk.
By understanding the strengths and applications of each tool, organizations can make well-informed choices that enhance quality control and improve decision-making. Selecting the appropriate tool not only streamlines the risk management process but also ensures that efforts are focused on achieving consistent, high-quality outcomes.
Six Sigma offers a variety of tools and frameworks specifically designed to help teams identify, analyze, and mitigate risks within processes. These tools are invaluable for organizations aiming to uphold high-quality standards, minimize errors, and enhance operational efficiency. Each tool serves a unique purpose, from prioritizing risks to understanding root causes, making it possible for teams to address potential issues before they impact performance proactively.
Selecting the right tool or combination of tools ensures that risk management efforts are aligned with organizational goals and capable of achieving measurable improvements. Below are some of the best Six Sigma tools and frameworks for effective risk analysis.
Failure Modes and Effects Analysis (FMEA) is a foundational tool in Six Sigma, widely recognized for its effectiveness in identifying potential risks within processes. This systematic approach involves a detailed examination of each process step to uncover failure modes possible ways a process could fail and their potential impacts on the operation. FMEA provides a structured method for assessing risks, allowing teams to rank them based on severity, occurrence, and detection likelihood, resulting in a Risk Priority Number (RPN).
By focusing efforts on high-RPN risks, organizations can prioritize which issues require immediate attention. This proactive risk management approach helps to prevent costly errors, enhances overall process reliability, and fosters a culture of continuous improvement by promoting thorough evaluations of each process component.
Root Cause Analysis (RCA) is a critical tool for identifying the underlying causes of problems within a process, making it essential for effective risk management. RCA employs techniques such as the "5 Whys" or Fishbone Diagrams to probe deeper into issues and uncover the root causes behind them. This tool is particularly effective in addressing recurring problems, as it focuses on eliminating the sources of risks rather than merely addressing the symptoms.
By implementing RCA, organizations can develop sustainable solutions that prevent future occurrences of the same issues. This thorough understanding of the root causes not only enhances team knowledge of process weaknesses but also drives continuous improvement by highlighting areas for further enhancement. Ultimately, RCA promotes a proactive approach to risk mitigation, ensuring that solutions are grounded in a comprehensive understanding of the processes involved.
Control Charts are powerful statistical tools that monitor process performance over time, providing insights into variations that could indicate potential risks. By plotting process data on a chart with established control limits, teams can visually track stability and quickly identify unusual deviations from the norm. When data points fall outside these control limits, it signals a potential risk of producing defects or inconsistencies within the process.
Control Charts are particularly valuable in processes requiring consistent outputs, as they allow teams to detect trends, shifts, or patterns in real-time. This proactive monitoring empowers organizations to intervene before issues escalate, thereby maintaining quality standards and minimizing variability-related risks. By utilizing Control Charts, teams can achieve a deeper understanding of process behavior, enabling them to implement corrective actions and enhance overall process reliability while fostering a culture of continuous improvement.
Pareto Analysis is a prioritization tool based on the 80/20 rule, which helps teams focus their efforts on the most significant risk factors affecting a process. By categorizing and analyzing issues, Pareto Analysis allows organizations to create a Pareto Chart, which visually represents the frequency of problems in descending order. This chart highlights the few critical causes that contribute to the majority of issues, enabling teams to concentrate their resources on addressing these high-impact risks.
The effectiveness of Pareto Analysis lies in its ability to simplify complex problems, directing attention toward areas that will yield the greatest improvements. By focusing on the most significant risk factors, organizations can enhance efficiency and effectiveness in their risk management strategies. This approach not only optimizes resource allocation but also fosters a culture of data-driven decision-making, ultimately contributing to improved process quality and operational excellence.
Fault Tree Analysis (FTA) is a structured risk assessment tool that visually represents potential failure points within a system or process. By creating a fault tree diagram, teams can map out the relationships between different events, starting from a central failure event and branching out into various causes that could lead to that failure. FTA is particularly valuable in complex systems, where multiple interrelated factors may contribute to potential risks.
This detailed visualization aids teams in understanding how various elements interact and helps trace risks back to their origins. By identifying these pathways, organizations can develop targeted risk-reduction strategies that enhance overall process resilience. FTA not only provides clarity on potential risk factors but also facilitates collaboration among team members, as they can engage in meaningful discussions about the implications of each identified risk, ultimately leading to more robust solutions and improved quality outcomes.
The Risk Assessment Matrix is a simple yet effective tool for categorizing and prioritizing risks based on their likelihood and potential impact. This tool enables teams to assign each identified risk a score, allowing them to plot the risks on a matrix that visually summarizes their priority levels. The matrix categorizes risks into low, medium, and high priority, facilitating easier allocation of resources and attention to the most pressing issues. Its versatility makes the Risk Assessment Matrix applicable to both straightforward and complex projects, promoting quick decision-making by providing a clear overview of risk levels.
By utilizing this matrix, organizations can ensure that their risk management efforts are strategically aligned with operational goals, thus optimizing resource allocation. The matrix serves as a valuable communication tool as well, helping teams present risk profiles to stakeholders effectively, ensuring transparency, and fostering a culture of proactive risk management throughout the organization.
Enterprise Risk Management (ERM) is a comprehensive framework that organizations use to identify, assess, manage, and monitor risks that could impact their objectives. The key components of ERM provide a structured approach for organizations to systematically address risks, ensuring they align with strategic goals while enhancing decision-making processes.
By integrating risk management into all aspects of the organization, ERM enables teams to proactively identify potential threats and opportunities, fostering a risk-aware culture. This holistic approach not only safeguards assets and resources but also enhances overall organizational resilience. Understanding the eight core components of ERM helps organizations implement effective risk management strategies that drive sustainable growth and success.
Six Sigma is a data-driven methodology aimed at improving business processes by minimizing variability and defects. It utilizes a structured approach that focuses on understanding customer needs and translating them into specific performance measures. The core philosophy of Six Sigma revolves around the idea that all processes have inherent variability, which can lead to defects if not properly managed. By employing statistical tools and techniques, Six Sigma practitioners analyze data to identify the root causes of problems, enabling organizations to implement targeted improvements that enhance overall quality and efficiency. This systematic approach fosters a culture of continuous improvement, empowering teams to make informed decisions based on empirical evidence.
At the heart of the Six Sigma methodology is the DMAIC framework, which stands for Define, Measure, Analyze, Improve, and Control. This five-step process guides organizations through the problem-solving journey, starting with clearly defining the project goals and identifying the customer requirements. Next, measurement tools are employed to collect relevant data, followed by analysis to identify root causes of defects. Once solutions are developed, they are implemented to improve the process, and control measures are established to sustain these improvements over time. By adhering to this rigorous framework, organizations can achieve significant reductions in defects, increase customer satisfaction, and ultimately drive business success.
The Six Sigma process of business transformation is a structured, data-driven approach that organizations utilize to enhance performance, improve quality, and streamline operations. By focusing on reducing defects and variability in processes, Six Sigma aims to create a significant impact on business outcomes. This methodology emphasizes a systematic framework that aligns organizational strategies with customer needs, ensuring that all efforts contribute to overall efficiency and effectiveness.
Through the application of statistical tools and techniques, organizations can identify opportunities for improvement and implement changes that foster sustainable growth. Six Sigma encourages a culture of continuous improvement, empowering employees at all levels to actively participate in the transformation process. The result is a more resilient organization that is better equipped to meet market demands, enhance customer satisfaction, and drive profitability.
The Define phase is the initial step in the Six Sigma process, where project goals, objectives, and scope are clearly articulated. This phase involves identifying the specific problem or opportunity that the organization aims to address and understanding its impact on customers and business performance. Key stakeholders are engaged to gather insights and ensure alignment on the project’s objectives.
This collaborative approach helps establish a clear project charter, which outlines the purpose, scope, timeline, and resources required for the initiative. By defining the problem accurately and involving relevant stakeholders, organizations set the foundation for successful project execution, ensuring that all efforts are focused on addressing the most critical issues.
In the Measure phase, organizations collect and analyze data to assess the current state of the process under investigation. This step is crucial for establishing a baseline performance level and identifying the specific metrics that will be used to gauge improvement. During this phase, teams gather quantitative and qualitative data related to the defined problem, employing various measurement tools and techniques.
Data analysis helps to uncover patterns and trends, providing insights into process variability and potential areas for improvement. By accurately measuring current performance, organizations can identify gaps between existing and desired outcomes, enabling them to make informed decisions about the necessary changes and interventions required to drive business transformation.
The Analyze phase involves a thorough examination of the data collected during the Measure phase to identify root causes of defects and process inefficiencies. This critical step employs various analytical tools and techniques, such as Pareto charts, fishbone diagrams, and regression analysis, to dissect the data and uncover underlying issues.
By understanding the factors contributing to variability and defects, organizations can prioritize areas for improvement based on their impact on overall performance. This phase emphasizes the importance of data-driven decision-making, ensuring that the proposed solutions are grounded in empirical evidence. By effectively analyzing the data, organizations can develop targeted strategies that address the root causes of problems, paving the way for meaningful process improvements.
In the Improve phase, organizations implement solutions aimed at addressing the root causes identified during the Analyze phase. This step involves brainstorming potential solutions, evaluating their feasibility, and selecting the most effective options for implementation. Pilot testing may be conducted to validate the proposed changes and assess their impact on process performance before full-scale implementation.
The Improve phase emphasizes collaboration and cross-functional teamwork, ensuring that all stakeholders are engaged in the change process. Once the improvements are implemented, organizations monitor their effectiveness through ongoing data collection and analysis, making necessary adjustments as needed. By focusing on continuous improvement, organizations can enhance operational efficiency and deliver greater value to customers.
The Control phase is the final step in the Six Sigma process, where organizations establish mechanisms to sustain the improvements achieved during the Improve phase. This step involves implementing control plans, monitoring performance metrics, and setting up regular review processes to ensure that the gains made are maintained over time. Training and communication play a vital role in embedding the changes into the organization’s culture, ensuring that employees understand and adhere to the new processes.
By establishing a robust control framework, organizations can proactively identify any deviations from desired performance levels and take corrective action before issues escalate. This commitment to ongoing monitoring and improvement reinforces the organization’s dedication to quality and operational excellence, ultimately driving long-term success and customer satisfaction.
Six Sigma techniques are a set of methodologies and tools that organizations employ to improve processes, enhance quality, and reduce defects. Rooted in statistical analysis, these techniques aim to identify and eliminate the causes of errors and inefficiencies within business processes. By fostering a culture of continuous improvement, Six Sigma empowers organizations to achieve higher levels of operational excellence, customer satisfaction, and profitability.
The techniques encompass a range of strategies, from basic quality management principles to advanced statistical tools, making them applicable across various industries and organizational contexts. Understanding and effectively applying these techniques enables teams to implement data-driven decision-making processes, which are crucial for sustaining improvements and driving business transformation. Here are ten essential Six Sigma techniques that organizations can leverage to enhance their performance and achieve their strategic objectives.
DMAIC is the foundational framework of Six Sigma, standing for Define, Measure, Analyze, Improve, and Control. This structured approach guides teams through problem-solving and process improvement initiatives. In the Define phase, project goals and scope are established, focusing on customer needs. The Measure phase involves collecting data to assess current performance and identify areas for improvement.
Next, the Analyze phase examines data to uncover the root causes of defects. In the Improve phase, solutions are developed and implemented to enhance the process, while the Control phase ensures that these improvements are sustained over time. By following the DMAIC methodology, organizations can systematically address challenges, leading to significant reductions in variability and defects and ultimately driving better business outcomes.
DMADV, which stands for Define, Measure, Analyze, Design, and Verify, is a Six Sigma technique specifically used for designing new processes or products. This methodology is particularly useful when existing processes are inadequate or when organizations aim to innovate. In the Define phase, project goals and customer requirements are identified. The Measure phase focuses on collecting data to determine critical quality characteristics.
The Analyze phase evaluates this data to identify design options that meet customer needs. In the Design phase, detailed designs are developed, followed by the Verify phase, where prototypes are tested to ensure they meet specifications. DMADV helps organizations create processes that are efficient, effective, and aligned with customer expectations, reducing the risk of defects and enhancing overall quality.
SIPOC is a high-level process mapping tool used in Six Sigma to visualize and understand the key elements of a process. The acronym stands for Suppliers, Inputs, Processes, Outputs, and Customers. This technique helps teams identify and document the flow of materials and information in a process, providing a comprehensive overview. In the SIPOC diagram, suppliers provide inputs that go through a defined process to produce outputs that are delivered to customers.
By creating a SIPOC diagram, organizations can clarify process boundaries, identify key stakeholders, and ensure that all team members have a shared understanding of the process. This visualization is particularly useful in the Define phase of DMAIC, as it sets the stage for more detailed analysis and improvement efforts.
The Fishbone diagram, also known as the Ishikawa or cause-and-effect diagram, is a tool used to identify and analyze the root causes of a problem. This visual representation resembles a fish's skeleton, with the head representing the problem and the bones representing various categories of potential causes, such as people, processes, materials, and equipment.
Teams brainstorm potential causes and categorize them on the diagram, facilitating discussions and encouraging comprehensive analysis. By using the Fishbone diagram, organizations can identify not only the direct causes of a problem but also contributing factors that may not be immediately obvious. This technique is particularly effective in the Analyze phase of DMAIC, helping teams prioritize issues to address in their improvement efforts.
Value Stream Mapping (VSM) is a Lean management technique used in conjunction with Six Sigma to analyze the flow of materials and information required to bring a product or service to the customer. This visual representation helps teams identify waste and inefficiencies within a process, facilitating continuous improvement efforts. VSM provides a clear picture of how value is added at each step, allowing organizations to pinpoint areas for enhancement.
By mapping the current state of the process and identifying desired future states, teams can develop actionable plans to optimize workflows, reduce lead times, and enhance customer satisfaction. This technique is especially valuable in the Measure and Improve phases of DMAIC, as it highlights both current performance and opportunities for improvement.
Kaizen, a Japanese term meaning "continuous improvement," is a philosophy that emphasizes the incremental enhancement of processes, products, and services within an organization. It involves all employees at every level and promotes a culture of teamwork, where everyone is encouraged to contribute ideas and suggestions for improvement. One of the key aspects of Kaizen is the focus on small, manageable changes that can lead to significant improvements over time.
Techniques such as Gemba Walks allow leaders to engage directly with frontline employees to identify challenges and gather insights. Standardized Work establishes clear procedures to ensure consistency and quality. Visual Management uses charts and dashboards to make important information accessible to all employees, facilitating quick decision-making. Additionally, Poka-Yoke or mistake-proofing techniques help prevent errors and defects by designing processes that eliminate the possibility of mistakes.
The 5 Whys technique is a simple yet powerful root cause analysis tool used in Six Sigma to identify the underlying causes of a problem. The process involves asking "why" repeatedly typically five times until the root cause is uncovered. This technique encourages teams to dig deeper beyond surface-level symptoms, fostering a culture of inquiry and critical thinking.
By systematically exploring the chain of causation, organizations can develop targeted solutions that address the fundamental issues rather than just treating the symptoms. The 5 Whys technique is particularly effective in the Analyze phase of DMAIC, enabling teams to uncover insights that drive meaningful process improvements.
Brainstorming is a collaborative technique used in Six Sigma to generate creative ideas and solutions for process improvement. This method encourages team members to share their thoughts freely without criticism or judgment, fostering an open and inclusive environment. During brainstorming sessions, participants can contribute various perspectives and insights, which can lead to innovative solutions that may have yet to be considered.
Once ideas are generated, the team can prioritize them based on feasibility and impact. By leveraging collective knowledge and creativity, organizations can identify unique approaches to address challenges and enhance overall performance. This technique is commonly used in both the Improve and Control phases of DMAIC to encourage continuous improvement.
Statistical Process Control (SPC) is a method used to monitor and control processes through the use of statistical techniques. This approach involves collecting and analyzing data to identify variations in process performance and determine whether a process is stable and predictable. SPC tools, such as control charts, help organizations track process metrics in real-time, enabling them to detect deviations from established standards.
By implementing SPC, organizations can proactively address potential issues before they escalate into significant problems. This technique fosters a culture of continuous improvement by encouraging teams to rely on data for decision-making and process optimization. SPC is integral to maintaining quality and efficiency, ensuring that processes remain within acceptable limits.
Control Plans are documented procedures that outline how to monitor and control processes to ensure consistent quality and performance. These plans detail the process specifications, measurement systems, and control methods that should be employed to maintain process stability. Control Plans help organizations identify critical process parameters and outline the actions to be taken if variations occur.
By implementing effective Control Plans, organizations can prevent deviations from desired performance levels, ensuring that improvements made during the DMAIC process are sustained over time. This technique is essential for maintaining long-term quality and process reliability, ultimately contributing to overall operational excellence.
Six Sigma tools and frameworks play a crucial role in risk analysis by providing methodologies for identifying, assessing, and mitigating risks within processes. These tools help organizations streamline operations, enhance quality, and drive continuous improvement by addressing potential issues before they escalate.
By leveraging the right tools, teams can foster a proactive culture of quality management, ensuring that processes align with customer expectations and operational goals. This strategic approach not only minimizes risks but also enhances overall performance, leading to increased customer satisfaction and operational excellence. Below are key Six Sigma tools that are particularly effective in risk analysis:
Six Sigma tools provide organizations with structured methodologies to improve processes, enhance quality, and reduce defects. These tools focus on data-driven decision-making, enabling teams to identify the root causes of problems and implement effective solutions. By utilizing Six Sigma, companies can achieve significant cost savings, increase efficiency, and enhance customer satisfaction.
Furthermore, the collaborative nature of Six Sigma promotes a culture of continuous improvement, involving employees at all levels in the pursuit of operational excellence. Ultimately, the adoption of Six Sigma tools can lead to sustainable improvements and a competitive advantage in the market.
Six Sigma is a data-driven methodology designed to improve processes by eliminating defects and ensuring quality. Within this framework, there are several defined levels of expertise, often categorized by belts, much like martial arts. Each level signifies a different degree of knowledge, skills, and experience in Six Sigma practices.
These levels range from White Belt, which provides a foundational understanding, to Black Belt, which signifies advanced proficiency and leadership in Six Sigma projects. By understanding the different Six Sigma levels, organizations can better align their training programs and project management strategies to achieve their quality improvement goals effectively.
Six Sigma professionals play a vital role in improving organizational processes and enhancing quality across various industries. As companies increasingly adopt Six Sigma methodologies to drive efficiency and reduce defects, the demand for qualified Six Sigma practitioners continues to grow. Career choices in this field are diverse, ranging from entry-level positions to advanced roles that require specialized knowledge and expertise.
Common job titles include Six Sigma Green Belt, Black Belt, Master Black Belt, and Quality Manager, among others. These positions offer varying responsibilities, which typically correlate with the level of Six Sigma certification held. Additionally, salary prospects for Six Sigma professionals can be lucrative, with compensation packages often reflecting experience, industry, and geographical location.
The Six Sigma technique for analyzing requirements serves as a vital tool in enhancing business processes and ensuring that customer needs are met with precision. By utilizing structured methodologies like DMAIC, organizations can systematically identify, measure, and improve critical requirements, leading to more efficient operations and higher-quality outputs.
Implementing these tools encourages collaboration across teams, fosters a culture of continuous improvement, and drives significant business outcomes. Ultimately, adopting Six Sigma techniques not only aligns product development with customer expectations but also strengthens the overall competitive advantage of an organization in today’s dynamic market environment.
Copy and paste below code to page Head section
Six Sigma is a data-driven methodology that focuses on improving process quality by reducing defects and variability. It uses statistical tools and techniques to analyze processes and implement improvements, leading to increased efficiency, cost savings, and enhanced customer satisfaction. Organizations adopt Six Sigma to achieve high-quality standards and continuous process enhancement.
While Six Sigma aims to minimize defects and reduce variability through data analysis, Lean focuses on eliminating waste and streamlining processes to enhance flow. Both methodologies prioritize efficiency and quality, and organizations often integrate them to achieve comprehensive process improvements, maximizing productivity while ensuring high standards in quality control.
Key Six Sigma tools include DMAIC (Define, Measure, Analyze, Improve, Control), DMADV (Define, Measure, Analyze, Design, Verify), SIPOC (Suppliers, Inputs, Process, Outputs, Customers), Fishbone Diagrams, and Value Stream Mapping. Each tool serves a unique purpose in the Six Sigma process, aiding teams in identifying problems, analyzing data, and implementing effective solutions.
Six Sigma certifications, such as Yellow Belt, Green Belt, Black Belt, and Master Black Belt, signify an individual’s proficiency in Six Sigma principles and methodologies. These certifications are tiered based on expertise, with higher levels indicating greater knowledge and leadership capabilities in Six Sigma projects and processes, enhancing career opportunities.
The time required to obtain Six Sigma certification varies depending on the level of certification and the training provider. Generally, it can take anywhere from a few weeks to several months to complete the necessary coursework, practical applications, and examinations, depending on the individual’s pace and commitment.
Yes, Six Sigma is a versatile methodology that can be applied across a wide range of industries, including manufacturing, healthcare, finance, and service sectors. Its principles and tools help organizations improve processes, reduce waste, and enhance quality, making it relevant for any industry seeking operational excellence.