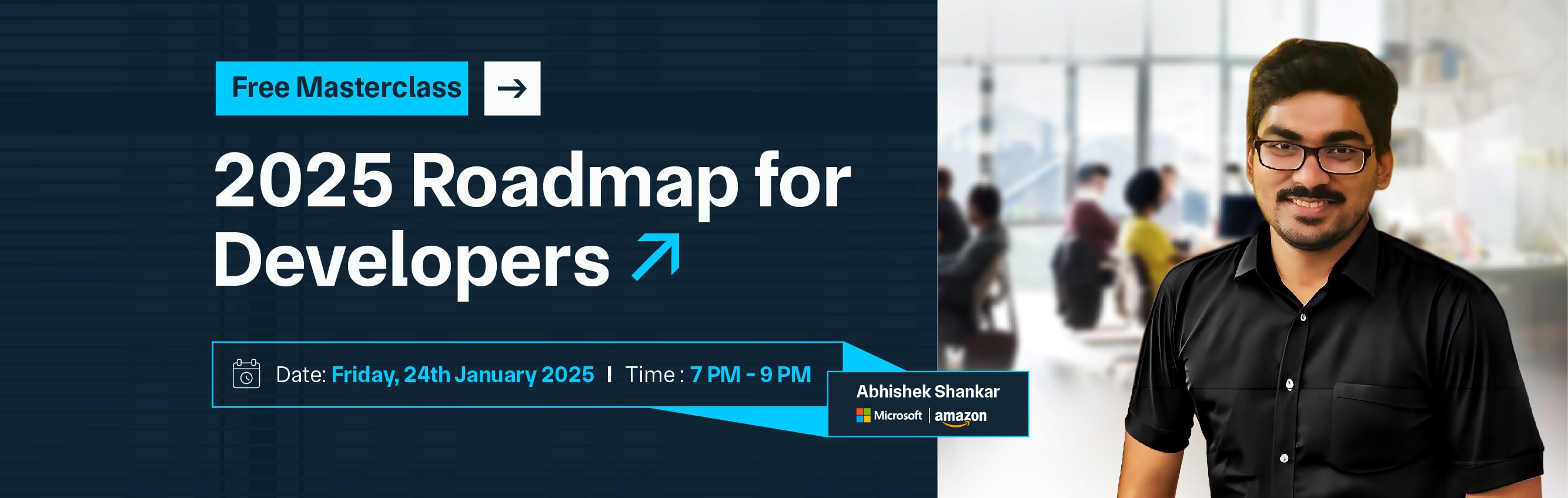
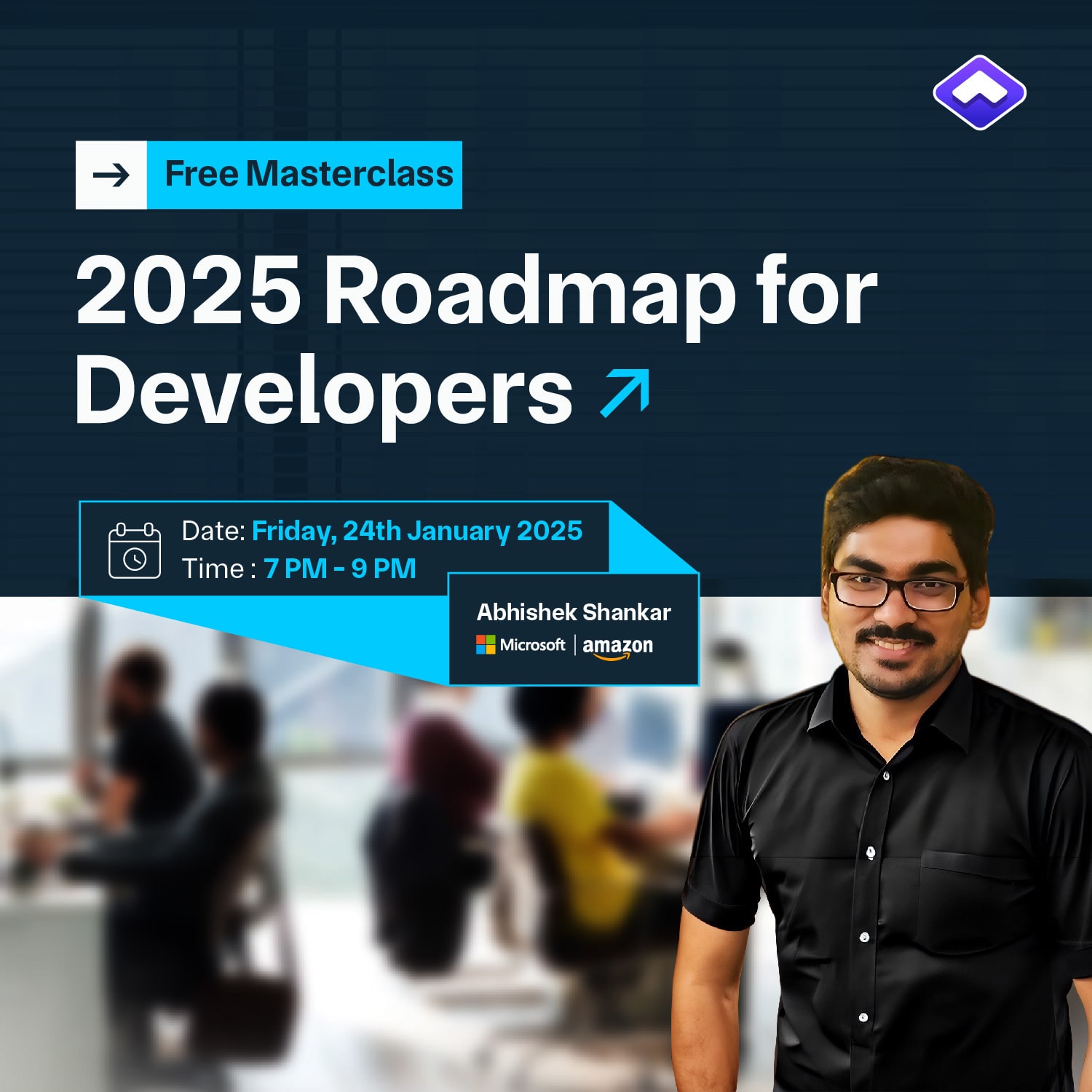
Six Sigma rule is a structured methodology designed to improve processes by minimizing defects and reducing variability. Originally developed by Motorola in the 1980s, it has become a widely adopted approach across industries to enhance performance, efficiency, and quality. Six Sigma focuses on identifying inefficiencies and errors in processes, analyzing their root causes, and implementing data-driven solutions to achieve sustainable improvements. The core objective of Six Sigma is to reduce defects to no more than 3.4 per million opportunities, equating to an impressive process efficiency of 99.99966%.
This is achieved through the DMAIC framework Define, Measure, Analyze, Improve, and Control. Each phase of DMAIC serves as a systematic guide for problem-solving and process optimization, ensuring that improvements are not only implemented but also sustained. By leveraging statistical tools, organizations can make informed, data-based decisions, driving better results across all areas of operation.
To improve process quality, Six Sigma enhances customer satisfaction, lowers operational costs, and increases profitability. It fosters a culture of continuous improvement, promoting collaboration and accountability. Whether used in manufacturing, healthcare, or service industries, Six Sigma equips organizations with the tools to achieve operational excellence and maintain a competitive edge in a constantly evolving market.
Six Sigma is a data-driven methodology used to improve processes by reducing defects and variations, aiming for near-perfection in quality. Originally developed by Motorola in the 1980s, it employs statistical analysis to identify and eliminate errors in a process, striving to achieve a defect rate of less than 3.4 per million opportunities. The primary focus of Six Sigma is to enhance performance by improving process efficiency and consistency. It integrates tools such as DMAIC (Define, Measure, Analyze, Improve, Control) and DMADV (Define, Measure, Analyze, Design, Verify) to streamline workflows and ensure quality at every stage.
Beyond its focus on statistical analysis, Six Sigma also promotes a cultural shift in organizations, encouraging continuous improvement and collaboration across departments. Practitioners are trained in various levels of expertise, such as Yellow, Green, and Black Belts, signifying their mastery in implementing Six Sigma strategies. By reducing waste, optimizing resources, and improving customer satisfaction, Six Sigma helps businesses achieve measurable financial gains and sustain long-term operational excellence.
Six Sigma’s core process improvement framework follows a structured methodology known as DMAIC, which stands for Define, Measure, Analyze, Improve, and Control. This method provides a clear, step-by-step approach to problem-solving and process optimization, focusing on data-driven decision-making. By following these five phases, organizations can systematically address inefficiencies, reduce variation, and eliminate defects.
DMAIC is particularly useful for improving existing processes and ensuring that changes are sustainable over time. Below is a detailed breakdown of each phase of the Six Sigma methodology, showing how they collectively contribute to achieving significant quality improvements and operational excellence.
The first step in Six Sigma is to Define the problem or process that needs improvement. This phase sets the foundation for the entire project, and it's essential to get it right. Here, teams work on clearly defining the scope of the problem by identifying what exactly needs to be fixed or optimized. The Define phase involves gathering input from stakeholders, customers, and team members to understand their expectations and needs.
The project charter, which is a key document, is created at this stage to outline the project’s objectives, timeline, and resources. Moreover, a high-level process map, called a SIPOC (Suppliers, Inputs, Process, Outputs, and Customers) diagram, is often developed to gain a holistic view of the process. The main goal is to ensure that everyone involved has a unified understanding of the problem and that the objectives are aligned with business goals and customer satisfaction.
In the Measure phase, the focus shifts to gathering data and assessing the current performance of the process under investigation. Accurate measurement is critical because it provides a fact-based foundation for analyzing the problem. First, teams must identify key performance indicators (KPIs) that reflect the process's effectiveness and efficiency. Next, they collect relevant data such as process times, defect rates, or customer feedback to establish a performance baseline. This baseline acts as a benchmark that will be used later to compare improvements.
Tools like data collection plans, measurement system analysis, and statistical techniques help ensure that the data is both reliable and valid. Additionally, this phase often includes creating detailed process flowcharts to visualize how the process operates. By the end of the Measure phase, the team should have a clear understanding of the process’s current state, including how much variation exists and where bottlenecks or inefficiencies are occurring.
The Analyze phase is where the team delves into the root causes of the problem. This is often the most analytical part of the Six Sigma process, requiring the use of statistical tools and data analysis techniques to pinpoint what’s driving defects or inefficiencies. The team starts by examining the data gathered in the Measure phase to identify trends, correlations, or unusual patterns that may reveal the root causes of variation. Common tools used in this phase include cause-and-effect diagrams (also known as fishbone or Ishikawa diagrams), Pareto charts, regression analysis, and hypothesis testing.
The team may also perform failure mode and effects analysis (FMEA) to assess potential failure points within the process. By thoroughly analyzing the process and its inputs, the team uncovers not only the symptoms of the problem but also the fundamental issues causing them. The Analyze phase concludes with the identification of critical areas for improvement, ensuring that the solutions developed in the next phase target the real problems, not just surface-level symptoms.
In the Improve phase, the focus shifts to finding and implementing effective solutions to the problems identified in the Analyze phase. This is where creativity meets data-driven decision-making. Teams brainstorm potential solutions, often involving cross-functional stakeholders, to generate ideas that can address the root causes. Once ideas are generated, they are rigorously tested for feasibility and effectiveness. The best solutions are piloted or simulated on a small scale to ensure they work as intended before full implementation.
During this phase, tools such as the Design of Experiments (DOE), pilot testing, and simulation modeling are often used to refine and optimize the solutions. This phase may also include process redesign, introducing new technologies, or retraining employees to follow improved workflows. The Improve phase is critical for ensuring that solutions not only fix the problem but also create long-term gains in efficiency, quality, and performance. The goal is to make sure that improvements are sustainable and that they deliver measurable results in terms of reduced defects, improved process speeds, and enhanced customer satisfaction.
The final step in Six Sigma, Control, is all about maintaining the gains achieved in the Improve phase. This phase ensures that the solutions and process improvements are sustained over time, preventing the process from reverting to its previous, inefficient state. To achieve this, the team implements control mechanisms such as standard operating procedures (SOPs), process control charts, and key performance indicator (KPI) monitoring systems. These tools allow the team to continuously track the performance of the process and quickly detect any deviations from the improved state.
Training is often provided to process owners and frontline employees to ensure they understand the changes and can consistently implement them. Additionally, a response plan is developed so that if any issues arise, they can be addressed quickly before they lead to significant problems. The Control phase is crucial because it turns the improvements into part of the organization's standard practices, ensuring long-term success and continuous improvement.
Six Sigma is a disciplined, data-driven methodology designed to improve the quality of processes by minimizing defects and variability. It stands out due to its focus on measurable outcomes and its structured approach to problem-solving. The framework uses statistical tools and techniques to identify inefficiencies, reduce waste, and enhance overall performance.
Six Sigma emphasizes continuous improvement, customer satisfaction, and a deep understanding of processes through quantifiable data. It is also characterized by its structured training system, where individuals earn certifications at various levels, such as Green Belts and Black Belts. Below are the key characteristics that define the Six Sigma methodology.
Lean Six Sigma is a powerful methodology that combines the principles of Lean Manufacturing and Six Sigma to optimize processes, enhance quality, and reduce waste. Lean focuses on streamlining operations by eliminating non-value-added activities and improving flow, while Six Sigma emphasizes reducing variation and defects through data-driven decision-making. Together, these approaches create a comprehensive framework that not only aims for efficiency but also ensures high-quality outputs.
Organizations that implement Lean Six Sigma benefit from a holistic strategy that addresses both speed and quality, making it particularly effective in industries such as manufacturing, healthcare, and service. The integration of Lean and Six Sigma fosters a culture of continuous improvement, empowering teams to identify and tackle inefficiencies proactively.
By utilizing tools such as Value Stream Mapping and DMAIC (Define, Measure, Analyze, Improve, Control), Lean Six Sigma provides a structured approach to problem-solving and process enhancement. This methodology not only focuses on immediate results but also encourages sustainable improvements that can lead to significant cost savings and increased customer satisfaction. Ultimately, Lean Six Sigma serves as a roadmap for organizations seeking to achieve operational excellence while delivering value to customers.
Six Sigma certification is a structured training program designed to equip individuals with the knowledge and skills necessary to implement Six Sigma methodologies effectively. The certification process typically involves various belt levels that signify a practitioner's expertise and ability to lead Six Sigma projects. Each belt level corresponds to different competencies, responsibilities, and the depth of understanding of Six Sigma tools and techniques.
The most common ranks are Yellow Belt, Green Belt, Black Belt, and Master Black Belt, with each level progressively requiring more knowledge and experience. These certifications not only enhance an individual's career prospects but also contribute to an organization's capability to achieve process improvements and operational excellence. Below is a table outlining the different Six Sigma certification levels and their key characteristics.
Six Sigma has been successfully implemented across various industries, leading to substantial improvements in quality, efficiency, and customer satisfaction. This methodology employs a data-driven approach to identify and eliminate defects in processes, resulting in enhanced operational efficiency and significant cost reductions. Organizations that adopt Six Sigma principles gain a competitive edge by leveraging statistical analysis and systematic problem-solving to make informed decisions.
The impact of Six Sigma extends beyond immediate financial benefits; it fosters a culture of continuous improvement, empowering employees to contribute to organizational goals actively. Notable companies from different sectors have adopted Six Sigma, showcasing its versatility and effectiveness. Below are some prominent real-world examples of organizations that have effectively utilized Six Sigma principles to achieve remarkable results.
General Electric (GE) is one of the most renowned examples of Six Sigma implementation. The company adopted Six Sigma in the 1990s under the leadership of then-CEO Jack Welch. GE implemented Six Sigma as part of its strategy to improve product quality and operational efficiency. By training thousands of employees in Six Sigma methodologies, GE was able to reduce defects in manufacturing processes and improve customer satisfaction.
The financial impact was significant, with estimates suggesting that GE saved over $2 billion in costs during the first few years of implementation. This success not only reinforced GE's reputation for quality but also positioned the company as a leader in operational excellence.
Motorola is credited with developing the Six Sigma methodology in the 1980s, initially as a response to increasing competition in the telecommunications industry. The company sought to improve product quality and reliability while reducing manufacturing costs. By employing Six Sigma tools, Motorola was able to decrease the defect rate in its production processes significantly. The initiative resulted in substantial savings and improved customer satisfaction.
Over the years, Motorola achieved an impressive milestone of reaching a defect rate of just 3.4 defects per million opportunities (DPMO). This achievement established Motorola as a pioneer in quality management and demonstrated the effectiveness of Six Sigma in driving operational improvements.
Toyota, known for its commitment to quality and efficiency, has effectively integrated Six Sigma principles into its production systems. The company's focus on continuous improvement, known as "Kaizen," aligns closely with Six Sigma methodologies. Toyota uses Six Sigma tools to analyze processes, eliminate waste, and enhance overall performance.
The application of these principles has led to significant reductions in manufacturing costs, improved product quality, and enhanced customer satisfaction. Toyota's implementation of Six Sigma has allowed the company to maintain its competitive edge in the automotive industry while consistently delivering reliable vehicles that meet customer expectations.
In the financial services sector, Bank of America adopted Six Sigma to enhance operational efficiency and improve customer service. The bank recognized the need to streamline processes and reduce errors in its transaction systems. By implementing Six Sigma methodologies, Bank of America was able to identify bottlenecks and inefficiencies in its operations.
The bank's Six Sigma initiatives led to reduced turnaround times for loan approvals and improved customer satisfaction scores. Additionally, the cost savings achieved through process improvements allowed Bank of America to invest further in technology and service enhancements, ultimately benefiting both the bank and its customers.
DHL, a global leader in logistics and express delivery, has utilized Six Sigma to optimize its operations and enhance customer satisfaction. The company implemented Six Sigma methodologies to analyze its supply chain processes, focusing on reducing delays and improving delivery accuracy. By leveraging data analysis and process mapping, DHL identified areas for improvement and implemented targeted solutions. The results were impressive, with significant reductions in delivery times and an increase in on-time delivery rates.
DHL's commitment to Six Sigma has not only improved its operational efficiency but also solidified its position as a customer-centric organization in the competitive logistics industry. These examples illustrate how Six Sigma can be effectively applied across diverse industries to drive significant improvements in quality, efficiency, and customer satisfaction. Organizations that embrace these methodologies often experience tangible benefits, positioning themselves for long-term success.
Six Sigma and Lean Six Sigma are two distinct methodologies used to improve processes, reduce waste, and enhance overall quality in organizations. While both approaches aim for operational excellence, they differ in focus, tools, and implementation strategies. Six Sigma primarily emphasizes reducing variation and defects through data-driven techniques and statistical analysis.
In contrast, Lean Six Sigma integrates Lean principles that prioritize eliminating waste and improving flow along with the rigorous problem-solving techniques of Six Sigma. Understanding these differences is essential for organizations looking to implement either methodology effectively. Below is a table summarizing the key differences between Six Sigma and Lean Six Sigma.
Six Sigma is grounded in a set of core principles that guide organizations toward achieving high-quality outputs and operational excellence. These principles are designed to foster a culture of continuous improvement and focus on understanding customer needs.
By adhering to these foundational concepts, businesses can systematically identify and eliminate defects, streamline processes, and enhance overall performance. The Six Sigma methodology empowers teams to make data-driven decisions and ensures that every employee plays a crucial role in driving quality initiatives. Below are the key principles of Six Sigma that serve as a framework for its implementation.
At the heart of Six Sigma is a commitment to understanding and meeting customer needs. Organizations prioritize customer satisfaction by identifying what is valuable to their clients and ensuring that products and services align with those expectations. This customer-centric approach involves gathering customer feedback and analyzing it to tailor processes that enhance customer experiences and foster loyalty.
By making the customer the focal point of all improvement efforts, companies ensure that their initiatives deliver real value. This principle emphasizes that understanding customer requirements and addressing them directly contributes to business success and drives overall performance improvement.
Six Sigma relies heavily on data to guide decision-making processes. By employing statistical analysis and quantitative measurements, organizations can identify trends, spot defects, and evaluate the effectiveness of changes made to processes. This principle advocates for evidence-based approaches rather than assumptions, ensuring that improvements are based on solid data.
Data-driven decision-making not only increases the accuracy of outcomes but also creates a culture of accountability within the organization. By integrating data analysis into daily operations, businesses can achieve more precise results and foster informed decision-making at all levels, ultimately leading to sustainable improvements in quality and efficiency.
A fundamental principle of Six Sigma is the focus on process improvement through systematic evaluation and optimization. By analyzing workflows and identifying inefficiencies, organizations can implement changes that streamline operations, reduce waste, and minimize errors. This principle emphasizes the importance of continual assessment, encouraging teams to challenge the status quo and seek out innovative solutions.
A commitment to process improvement ensures that organizations remain competitive and responsive to changing market demands. This involves not just fixing existing problems but also proactively seeking opportunities to enhance performance and efficiency, leading to better quality products and services that meet customer expectations.
Six Sigma aims to reduce variation in processes, which is essential for achieving consistent quality. Understanding the sources of variation allows organizations to implement controls that stabilize processes and minimize defects. This principle emphasizes the need to identify, analyze, and control variations to maintain high standards of quality.
By focusing on reducing variability, organizations can ensure that products and services consistently meet customer expectations, leading to increased satisfaction and trust. This process also includes employing statistical tools to quantify variation and develop strategies that promote consistency, which is crucial for achieving Six Sigma quality levels.
Effective Six Sigma initiatives require collaboration among various departments and functions within an organization. This principle recognizes that quality improvements often involve multiple areas of expertise, necessitating teamwork and communication. By fostering a collaborative environment, organizations can leverage diverse perspectives and skills to address complex challenges.
Cross-functional collaboration enhances problem-solving capabilities and encourages a holistic approach to process improvement. It breaks down silos and fosters a culture where all employees, regardless of their roles, are engaged in the quality improvement process. This collaborative spirit is vital for driving successful Six Sigma projects and ensuring that improvements are sustainable across the organization.
Continuous improvement is a core tenet of Six Sigma, encouraging organizations to pursue ongoing enhancement of their processes, products, and services. This principle emphasizes the need for a proactive approach to identifying opportunities for improvement, even after achieving initial successes. By instilling a culture of continuous improvement, organizations empower employees to seek out new methods, embrace change, and drive innovation.
This commitment ensures that organizations remain agile and competitive in an ever-evolving business landscape. Continuous improvement is not a one-time effort but rather an ongoing journey that requires dedication, focus, and the willingness to adapt to new challenges and opportunities.
Leadership involvement is crucial for the successful implementation of Six Sigma principles within an organization. Leaders set the tone for quality initiatives and play a pivotal role in fostering a culture of excellence. By actively participating in Six Sigma projects, providing resources, and supporting employee training, leaders demonstrate their commitment to quality improvement.
This principle highlights the importance of strong leadership in driving change, aligning organizational goals with Six Sigma objectives, and ensuring that all team members understand their roles in the improvement process. When leadership is engaged, it inspires teams to pursue excellence and creates a supportive environment for continuous improvement.
Employee empowerment is a significant principle of Six Sigma that emphasizes the importance of involving all employees in the quality improvement process. Organizations that empower their employees encourage them to take ownership of their work and contribute ideas for improving processes. This principle fosters a sense of responsibility and accountability among team members, leading to higher engagement levels and increased job satisfaction.
By providing training, resources, and a supportive environment, organizations enable employees to develop their skills and contribute effectively to Six Sigma initiatives. Empowered employees are more likely to identify problems, suggest innovative solutions, and actively participate in achieving quality objectives, ultimately benefiting the organization as a whole.
Motorola introduced the Six Sigma methodology in the 1980s as a response to increasing competition and the need for higher quality in manufacturing processes. The term "Six Sigma" refers to the statistical concept that measures a process's ability to produce a defect-free output, aiming for no more than 3.4 defects per million opportunities. This innovative approach was pioneered by engineer Bill Smith at Motorola, who recognized that traditional quality control methods needed to be revised to achieve the level of precision and reliability required in their products.
The success of Six Sigma at Motorola led to widespread adoption across various industries, including electronics, automotive, and healthcare, transforming the landscape of quality management. Central to the Six Sigma methodology is the DMAIC framework, which stands for Define, Measure, Analyze, Improve, and Control. Each phase plays a critical role in systematically improving processes and ensuring high quality. The Define phase focuses on clearly identifying the problem and establishing project objectives. During the Measure phase, teams collect and analyze data to understand current process performance.
The Analyze phase involves pinpointing the root causes of defects and inefficiencies. In the Improve phase, teams develop and implement solutions aimed at eliminating those root causes. Finally, the Control phase ensures that improvements are sustained over time by monitoring processes and implementing control mechanisms. Through this structured approach, organizations can achieve significant enhancements in quality, reduce costs, and ultimately enhance customer satisfaction.
Six Sigma employs a variety of techniques designed to identify and eliminate defects, reduce process variation, and enhance overall quality. These techniques are essential for implementing the DMAIC framework and are often tailored to specific industries or challenges.
By applying these methods, organizations can achieve significant improvements in their processes, leading to increased efficiency and customer satisfaction. The techniques involve statistical analysis, process mapping, and problem-solving tools, allowing teams to make data-driven decisions. Here are some of the key Six Sigma techniques utilized in organizations:
The DMAIC (Define, Measure, Analyze, Improve, Control) framework is a structured problem-solving methodology that guides teams through process improvement initiatives. Each phase serves a specific purpose, starting with defining the problem and project goals. In the Measure phase, relevant data is collected to assess current performance, providing a baseline for understanding the extent of the issues at hand.
The Analyze phase focuses on identifying the root causes of defects and determining their impact on process performance. Once the root causes are identified, the Improve phase implements solutions designed to eliminate these defects, optimizing the process for better quality outcomes. Finally, the Control phase ensures that sustained improvements are maintained by putting monitoring and control mechanisms in place, allowing for ongoing evaluation and adjustments as necessary.
Root Cause Analysis is a systematic problem-solving technique used to identify the fundamental cause of defects or issues within a process. By employing various tools like the "5 Whys" technique and Fishbone diagrams, teams can delve deeper into problems and discover the underlying issues that lead to defects. This analytical approach goes beyond treating symptoms, as it addresses the root causes to prevent recurrence effectively.
By resolving these fundamental problems, organizations can implement lasting solutions that significantly improve process performance and product quality. RCA not only enhances operational efficiency but also fosters a culture of accountability, where employees feel empowered to take ownership of quality issues and contribute to sustainable improvements.
Statistical Process Control is an essential technique in Six Sigma that involves using statistical methods to monitor and control a process. This method employs control charts to visualize process performance over time, helping teams identify variations, trends, and any deviations from expected performance levels. By analyzing this data, organizations can determine if a process is operating within acceptable limits or if corrective actions are needed.
SPC enables proactive management of processes by allowing teams to identify potential issues before they escalate into significant problems. This technique promotes consistency and stability in output quality, ensuring that processes are maintained at optimal performance levels. Ultimately, SPC contributes to higher quality products and services, reducing waste and increasing customer satisfaction.
Process mapping is a powerful visual representation tool used to outline the steps involved in a process, providing a clear understanding of workflows and interactions. This technique helps teams identify inefficiencies, bottlenecks, and areas for improvement by mapping out each stage of a process in detail. By visualizing processes, organizations can facilitate communication among team members and ensure that everyone understands their roles and responsibilities.
This clarity is essential for streamlining operations, as it allows for the identification of redundant steps and opportunities for automation. Additionally, process mapping helps ensure that all aspects of the process align with quality objectives, fostering collaboration and driving collective efforts toward continuous improvement.
Failure Mode and Effects Analysis is a systematic technique used to evaluate potential failure modes within a process and their impact on product quality. FMEA involves identifying possible failure points, assessing their likelihood and consequences, and prioritizing them based on risk. By focusing on high-risk failure modes, organizations can implement corrective measures proactively to enhance process reliability and reduce defects.
This technique not only improves product quality but also minimizes the potential for costly recalls and customer dissatisfaction. FMEA fosters a proactive culture of quality assurance, where potential issues are addressed before they become significant problems, ensuring that products consistently meet or exceed customer expectations.
Lean tools, such as 5S, Kaizen, and Value Stream Mapping, are often integrated with Six Sigma techniques to enhance process efficiency and eliminate waste. These tools focus on optimizing workflow and ensuring that resources are utilized effectively. For instance, the 5S methodology emphasizes workplace organization and standardization, promoting a clean and efficient working environment.
Meanwhile, Value Stream Mapping provides a comprehensive visualization of the flow of materials and information throughout a process, allowing teams to identify and eliminate non-value-added activities. By combining Lean principles with Six Sigma methodologies, organizations can achieve comprehensive process improvements that not only enhance quality but also foster a culture of continuous improvement and operational excellence.
Control charts are vital statistical tools used in Six Sigma to monitor process stability and variation over time. They provide a graphical representation of process data, helping teams identify trends and variations that may indicate potential problems. By setting control limits based on historical data, teams can quickly assess whether a process is in control or if deviations require investigation.
This proactive approach allows organizations to make timely interventions and adjustments to maintain quality standards. Control charts play a crucial role in sustaining improvements, ensuring that processes consistently produce desired outcomes and that any shifts in performance are addressed promptly. Their use not only enhances process reliability but also strengthens overall quality management practices.
Design of Experiments is a powerful statistical technique that helps teams understand the relationships between different variables affecting a process. By systematically varying inputs and observing the resulting changes in outputs, teams can identify optimal conditions and interactions that lead to improved performance. DOE allows organizations to conduct experiments efficiently, minimizing the number of trials required to achieve reliable results.
This technique is particularly valuable in product development and process optimization, enabling data-driven decisions that enhance quality and performance. By leveraging DOE, organizations can innovate and refine processes with greater confidence, ultimately leading to superior products and services that meet customer expectations.
Voice of the Customer refers to the process of capturing customers' needs, preferences, and feedback to inform product development and service delivery. Understanding the VoC is crucial for organizations looking to align their offerings with customer expectations. Techniques such as surveys, interviews, and focus groups are commonly used to gather this information.
By prioritizing customer insights, organizations can make informed decisions that drive improvements and ensure that their products and services consistently meet or exceed customer demands. This customer-centric approach is integral to Six Sigma, as it emphasizes the importance of quality in relation to customer satisfaction and loyalty.
Poka-Yoke, or mistake-proofing, is a technique used to prevent errors and defects in processes by designing systems that make it impossible for mistakes to occur or that immediately alert operators when an error is about to happen. This approach aims to enhance process reliability and product quality by proactively identifying potential failure points and implementing simple, effective solutions.
By integrating Poka-Yoke mechanisms into workflows, organizations can significantly reduce the likelihood of defects and improve overall quality outcomes. This not only enhances process reliability but also fosters a culture of quality consciousness among employees, encouraging them to take ownership of their work and contribute to continuous improvement initiatives.
Six Sigma tools are essential components of the methodology, providing the necessary techniques for process improvement and quality management. These tools help teams analyze data, identify root causes of defects, and implement solutions that enhance overall process efficiency.
By leveraging these tools, organizations can achieve measurable improvements in quality and performance, leading to increased customer satisfaction and reduced operational costs. Six Sigma tools are versatile and can be adapted to various industries and organizational needs. Here are some of the key Six Sigma tools utilized by teams to drive improvements:
Six Sigma professionals are in high demand across various industries as organizations strive to enhance their quality management processes and operational efficiency. With a focus on data-driven decision-making and continuous improvement, careers in Six Sigma can lead to rewarding opportunities in manufacturing, healthcare, finance, and beyond. Professionals with Six Sigma certifications often hold positions that require strong analytical skills and a thorough understanding of quality management principles.
Career choices range from process improvement specialists to quality managers and even executive roles like Chief Quality Officer (CQO). Salary prospects for Six Sigma professionals can vary widely based on factors such as experience, industry, and geographical location. The following table outlines common Six Sigma career choices along with their average salary ranges:
The DMADV (Define, Measure, Analyze, Design, Verify) methodology is a key framework within the Six Sigma approach, primarily used for developing new processes or products at a high-quality level. Unlike the DMAIC (Define, Measure, Analyze, Improve, Control) approach, which focuses on improving existing processes, DMADV is employed when the existing process is inadequate or when creating a new process is necessary.
This methodology emphasizes understanding customer requirements and ensuring that designs meet those specifications to deliver optimal performance. By following the DMADV framework, organizations can systematically evaluate their design processes, ensuring that every aspect meets quality standards and customer expectations before implementation. Below are the key phases of the DMADV methodology:
The Six Sigma Rule is a powerful framework that organizations can adopt to enhance their processes, minimize defects, and improve overall quality. By focusing on data-driven decision-making and continuous improvement, Six Sigma empowers teams to identify the root causes of issues and implement effective solutions. The methodology's structured approach, encompassing the DMAIC and DMADV frameworks, allows for both process optimization and new design creation.
Ultimately, the Six Sigma Rule fosters a culture of excellence within organizations, leading to increased efficiency, reduced costs, and heightened customer satisfaction. Embracing Six Sigma principles can significantly contribute to long-term success and competitive advantage in today’s dynamic business landscape.
Copy and paste below code to page Head section
Six Sigma is a data-driven methodology aimed at improving process quality by identifying and eliminating defects. It employs various statistical tools and techniques to analyze processes, enhance performance, and ensure that customer needs are met consistently.
The key components of Six Sigma include the DMAIC framework (Define, Measure, Analyze, Improve, Control) for improving existing processes and the DMADV framework (Define, Measure, Analyze, Design, Verify) for creating new processes. Additionally, Six Sigma relies on statistical analysis, quality management principles, and a focus on customer satisfaction.
Six Sigma certification demonstrates a professional's expertise in quality management and process improvement methodologies. It can enhance career prospects, increase earning potential, and provide organizations with skilled individuals capable of driving improvement initiatives.
Six Sigma offers several belt levels, including White Belt, Yellow Belt, Green Belt, Black Belt, and Master Black Belt. Each level represents varying degrees of knowledge, responsibility, and expertise in Six Sigma methodologies and practices.
Implementing Six Sigma can lead to reduced operational costs, improved process efficiency, increased customer satisfaction, and enhanced product quality. Organizations that adopt Six Sigma principles can achieve measurable improvements that contribute to overall business success.
Six Sigma can be applied across various industries, including manufacturing, healthcare, finance, telecommunications, and service sectors. Its versatility makes it an effective approach for any organization seeking to enhance quality and operational performance.