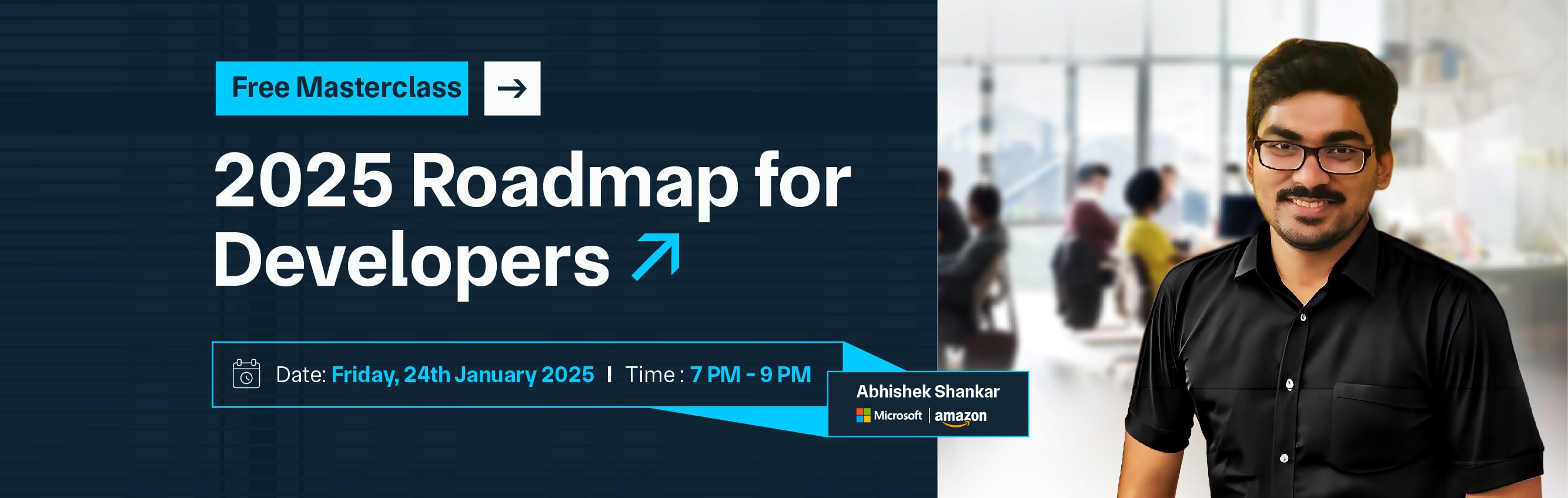
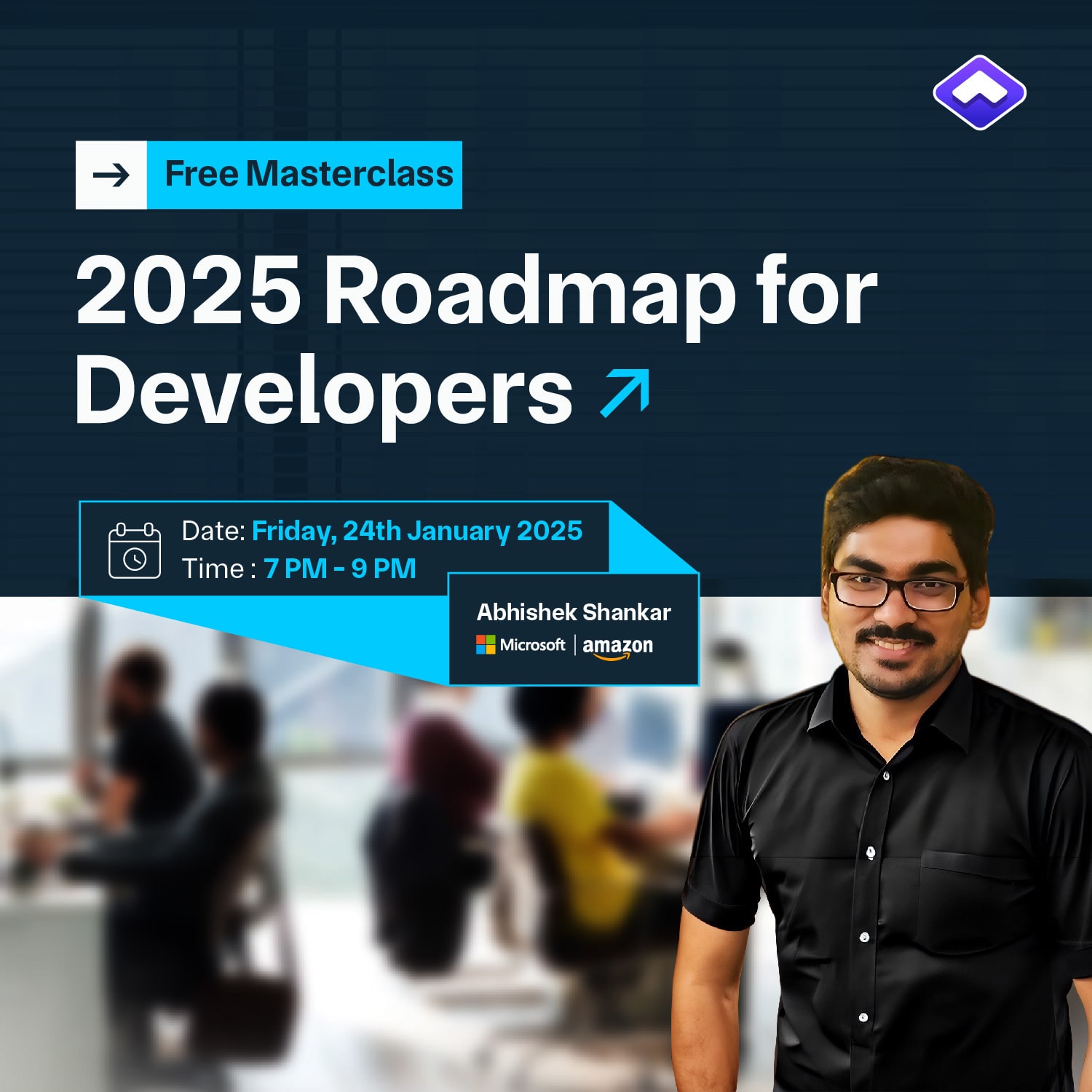
Kanban is a systematic approach to managing workflows that focuses on visualizing tasks and optimizing processes to enhance efficiency. The term "Kanban," which means "signboard" or "visual signal" in Japanese, highlights its reliance on visual tools such as boards and cards to track progress. This method originated in the manufacturing sector, particularly at Toyota, where it was designed to implement just-in-time (JIT) production.
By ensuring tasks are only started when needed, Kanban minimizes waste and prevents overproduction, creating a streamlined and responsive workflow. The Kanban methodology operates on core principles such as limiting work in progress and promoting continuous improvement. It allows teams to identify inefficiencies, balance workloads, and adapt to changing priorities with ease.
Its visual nature enhances team communication and collaboration, ensuring everyone stays aligned on project goals. Today, Kanban is not limited to manufacturing; it is widely adopted in software development, healthcare, and other industries where efficient task management is crucial. By enabling businesses to deliver value consistently, Kanban remains a trusted and versatile system for optimizing performance in a dynamic and competitive environment.
Kanban is a dynamic and highly adaptable framework that emphasizes the continuous flow of work and operational efficiency. To achieve these goals, Kanban relies on a set of core practices designed to streamline processes, improve visibility, and foster collaboration among teams. These practices, derived from lean manufacturing principles, focus on visualizing workflows, limiting work in progress, and creating a culture of continuous improvement.
By adhering to these core practices, teams can reduce waste, improve productivity, and deliver higher value to customers. Whether applied in manufacturing, software development, or service industries, Kanban’s core practices are designed to empower teams to work smarter, not harder.
They provide a structured yet flexible approach to managing tasks and identifying inefficiencies. Each practice works in harmony with the others, creating an integrated system that enhances agility, adaptability, and accountability. Below are the key practices of Kanban, explained in detail to help you understand how they drive success.
A Kanban board is a visual tool used to manage workflows and track progress across different stages of a process. It is a central element of the Kanban methodology, designed to enhance transparency, organization, and efficiency. The board typically consists of columns representing various stages, such as "To Do," "In Progress," and "Completed," and uses cards to signify individual tasks.
This system allows teams to visualize their workload, prioritize tasks, and identify bottlenecks quickly. Kanban boards are highly adaptable and can be customized to fit any industry or team size. Whether used in manufacturing, software development, or service delivery, they provide a simple yet powerful way to streamline processes and improve collaboration.
By offering real-time insights into workflow status, Kanban boards empower teams to make informed decisions and maintain steady progress. Below are the essential components and benefits of a Kanban board, explained in detail.
Electronic Kanban (e-Kanban) systems are digital tools designed to streamline workflow management by automating the traditional Kanban process. These systems use software platforms to create virtual Kanban boards, allowing teams to track tasks, monitor progress, and visualize workflows in real time. E-Kanban enhances the flexibility of the traditional method, providing instant updates and notifications to team members, regardless of their location.
This automation simplifies task management, boosts productivity, and reduces the reliance on physical boards, offering teams the ability to manage complex projects more efficiently. In addition to providing real-time tracking, e-Kanban systems can be integrated with various enterprise tools such as inventory management, enterprise resource planning (ERP), and customer relationship management (CRM) systems.
This integration enables seamless data exchange, improving communication and reducing manual data entry. Furthermore, e-Kanban systems offer advanced analytics and reporting features, helping teams identify bottlenecks, assess performance, and implement continuous improvements. With customizable workflows and enhanced collaboration features, e-Kanban offers a scalable, secure, and environmentally friendly solution for modern organizations looking to optimize their processes.
Scrum and Kanban are both popular Agile frameworks used for managing workflows and improving productivity. While both focus on delivering incremental improvements, they follow different principles and processes. Scrum is a structured framework that works in fixed-length iterations called sprints, where a specific amount of work is completed within a set period.
It includes clearly defined roles such as Scrum Master, Product Owner, and Development Team and prescribes ceremonies like Sprint Planning, Daily Stand-ups, and Retrospectives. Kanban, on the other hand, is a flexible, visual method for managing work, where tasks flow through stages on a Kanban board. It emphasizes continuous delivery with a focus on limiting Work in Progress (WIP) to avoid overloading the team.
While Scrum provides a structured, time-boxed approach to project management, Kanban offers more flexibility and allows for a continuous flow of work. Choosing between Scrum and Kanban depends on the team's needs, the type of project, and the level of flexibility required. Below is an expanded table comparing Scrum and Kanban based on various factors:
Kanban is a powerful workflow management system that helps teams visualize their tasks and optimize their processes. Originally developed for manufacturing, Kanban is now widely used in various industries to improve efficiency, reduce waste, and enhance collaboration.
The Kanban method allows teams to manage their work in real time, providing clear visibility into task status and progress. This leads to smoother workflows, better communication, and the ability to identify bottlenecks early. In turn, it helps improve overall productivity, reduce delays, and ensure a more sustainable approach to work management. Below are the key benefits of implementing Kanban:
While Kanban offers many benefits, it also has certain drawbacks that may impact its effectiveness depending on the nature of the team or project. One of the main challenges is that Kanban does not provide a specific structure for roles and responsibilities, which can lead to confusion in teams lacking clear leadership.
Additionally, because Kanban is highly flexible, it can be difficult to manage larger teams or projects with complex workflows. Without clear planning or deadlines, some teams may struggle with prioritizing tasks effectively. Below are some of the key disadvantages of using Kanban:
Kanban is often associated with both Agile and Lean methodologies, but it is primarily a Lean tool that incorporates Agile principles. The core principles of Kanban, such as limiting work in progress (WIP), visualizing workflow, and improving continuous flow, stem from Lean manufacturing practices, which focus on reducing waste and maximizing efficiency. Lean emphasizes the importance of streamlining processes, eliminating bottlenecks, and improving overall workflow to deliver value with minimal waste.
Kanban aligns closely with these Lean principles, as it helps teams optimize their processes by focusing on flow, efficiency, and continuous improvement. At the same time, Kanban is also used within Agile frameworks, especially in software development. Agile methodologies prioritize flexibility, iterative development, and responding to change.
Kanban's ability to adapt to changing work priorities, track tasks in real-time, and adjust workflow based on feedback makes it compatible with Agile practices. It provides a flexible, visual way of managing tasks, which is essential in Agile environments. Thus, while Kanban originated from Lean, it shares principles with Agile and can be used in conjunction with Agile to improve team performance and workflow management.
The Kanban system is a structured workflow management approach designed to increase productivity and reduce inefficiencies. Originating in Toyota’s manufacturing processes, it has since evolved into a versatile framework used across industries. Kanban focuses on visualizing workflows, setting clear work-in-progress (WIP) limits, and prioritizing tasks based on demand.
By emphasizing incremental improvements and collaboration it aligns teams to deliver value effectively. At its core, Kanban organizes tasks into manageable stages displayed on a Kanban board. Tasks move from “To Do” to “In Progress” and “Completed” as they advance.
This real-time visibility promotes accountability and identifies bottlenecks, ensuring smooth workflows. The system also embraces adaptability, allowing teams to refine processes continuously. Below is a detailed breakdown of Kanban’s principles:
Kanban divides workflows into detailed, adaptable stages that cater to specific needs. A Kanban board typically comprises columns like “Material Procurement,” “Initial Assembly,” “Testing,” and “Packaging.” This segmentation simplifies complex processes by breaking them into smaller, manageable steps. Teams can add or adjust columns to reflect real-time demands or changes in workflow priorities. For example, if a quality assurance stage becomes crucial due to increased defects, a “Quality Inspection” column can be introduced.
Dynamic segmentation ensures that every aspect of the process is visualized and monitored, creating opportunities to identify inefficiencies. This flexibility also benefits operations like product development or service delivery, where tasks are often interdependent. Moreover, such segmentation encourages proactive collaboration, as every team member knows their role in advancing tasks to the next stage, thereby enhancing productivity and transparency in the workplace.
Kanban boards utilize visual cues to prioritize tasks effectively, ensuring high-priority items are completed promptly. Tasks are often represented as cards and can include color codes or labels to highlight urgency or category. For instance, red cards might signify urgent tasks, green for standard tasks, and yellow for tasks needing further clarification. These visual indicators help teams quickly assess which tasks require immediate attention.
For example, in manufacturing, rush orders can be marked in red, ensuring they are processed ahead of routine tasks. The visual nature of Kanban ensures that priorities are clear to all team members, reducing confusion and miscommunication. This approach also supports better time management, as workers can focus their efforts on critical tasks without getting overwhelmed by less urgent ones. Over time, prioritization through visual cues fosters a culture of efficiency and accountability, enabling teams to deliver high-quality outcomes consistently.
Kanban supports the management of parallel workflows, enabling teams to handle multiple projects or tasks simultaneously. For instance, in manufacturing, a factory may produce multiple product lines, each with distinct workflows. A Kanban board can create separate lanes or swimlanes for each product, ensuring tasks within those workflows remain organized and do not interfere with one another.
Parallel workflows improve multitasking capabilities, reduce waiting times, and optimize resource allocation. For example, a factory producing both furniture and electronics can maintain separate workflows for assembly, quality control, and shipping. This separation prevents confusion and allows teams to specialize in their respective tasks. Additionally, parallel workflows make it easier to track progress across different projects, providing managers with a clear overview of performance. This clarity is especially beneficial in high-pressure environments, where balancing multiple priorities is critical to meeting deadlines and maintaining quality standards.
A fundamental aspect of Kanban is its pull-based system, where tasks are initiated only when there is demand or capacity downstream. This approach contrasts with traditional push systems, which can result in overproduction or resource wastage. For example, in manufacturing, a “signal” from the assembly line triggers material requisition or task initiation. This ensures that production aligns with actual needs rather than speculative forecasts.
The pull system reduces inventory costs, as only the required amount of materials is used. Moreover, it enhances workflow balance by preventing the overburdening of resources or team members. By focusing on demand-driven work, the pull system helps organizations adapt quickly to changing priorities without causing workflow disruptions. Over time, this approach improves efficiency and fosters a culture of responsiveness, making it a cornerstone of Kanban’s success across industries.
Kanban’s flexibility shines in its ability to adapt to real-time demand. Unlike rigid systems, Kanban allows teams to respond to fluctuating priorities dynamically. For instance, if a surge in orders for a specific product occurs, the Kanban board can be adjusted to prioritize its production. In a manufacturing context, this could mean temporarily reallocating resources, such as machinery or personnel, to meet urgent demands.
This adaptability ensures that customer needs are met promptly while maintaining the integrity of ongoing workflows. Real-time adjustments are made without overwhelming team members, as the system’s WIP limits prevent excessive multitasking. Additionally, by focusing on immediate needs, Kanban minimizes waste, ensuring that resources are utilized effectively. Over time, the ability to adapt quickly to demand changes builds resilience within the organization, making it well-equipped to handle market fluctuations or unexpected challenges.
Kanban naturally promotes collaboration by providing a shared visual framework where all team members can see the workflow and their roles within it. Tasks are clearly assigned, and progress is transparent, fostering a sense of ownership and responsibility. For example, in a manufacturing team, operators, quality inspectors, and managers can collaborate to ensure that tasks move smoothly from one stage to the next.
The shared understanding of priorities and progress minimizes misunderstandings and enhances communication. Kanban boards also serve as a platform for discussing bottlenecks and brainstorming solutions, further strengthening team cohesion. By creating a culture of accountability and cooperation, Kanban helps teams work more efficiently and harmoniously, ultimately delivering better results.
Kanban encourages continuous monitoring and iterative improvement. Teams regularly analyze metrics such as cycle time, throughput, and bottlenecks to refine workflows. For instance, if delays frequently occur in the assembly stage, managers can investigate and implement corrective measures, such as additional training or resource allocation.
By constantly monitoring workflows, teams can identify inefficiencies and implement small, incremental changes that improve overall performance. This focus on continuous improvement ensures that processes remain optimized and aligned with organizational goals. Over time, this approach helps build a culture of excellence where teams are consistently striving to deliver better results.
Modern Kanban systems leverage digital tools to enhance efficiency and accessibility. Digital boards provide real-time updates, analytics, and remote access, making them invaluable for distributed teams or large-scale operations. For example, a manufacturing supervisor can track workflows across multiple plants using a centralized digital dashboard.
Digital tools also integrate with other systems, such as ERP or inventory management software, ensuring seamless data exchange and better decision-making. This technological integration makes Kanban more versatile and effective, enabling teams to stay connected and responsive in fast-paced environments.
Kanban, a crucial component of Lean manufacturing, helps to optimize production processes by improving the flow of work, reducing waste, and increasing efficiency. It focuses on visualizing workflows and controlling work in progress (WIP) to ensure tasks are completed at the right time without overburdening resources.
By streamlining inventory management, production cycles, and communication, Kanban supports Lean principles like waste reduction and continuous improvement. Here are new points about Kanban in Lean manufacturing:
Kanban has become a vital tool for organizations striving to optimize workflow, minimize waste, and enhance productivity. Originating from Toyota’s Just-In-Time manufacturing philosophy, it is now widely adopted across diverse industries.
By using visual boards, Kanban helps companies manage tasks effectively and maintain operational transparency. Its real-world applications demonstrate its flexibility, from streamlining assembly lines in manufacturing to improving software development processes. Companies use Kanban to address unique challenges, such as inventory management, task prioritization, and quality control.
For instance, tech companies like Google and Apple use it to enhance collaboration, while manufacturers like Tesla and Ford rely on Kanban for efficiency in production. It allows organizations to adapt to shifting demands while maintaining high standards.
Tesla has revolutionized electric vehicle manufacturing using Kanban to maintain efficiency across its Gigafactories. The system helps track essential materials like lithium-ion batteries and semiconductor chips, which are critical to production. Kanban boards visualize real-time workflows, from inventory replenishment to assembly line progress.
Tesla’s innovative approach has reduced production bottlenecks and improved responsiveness to supply chain challenges. For example, during the COVID-19 pandemic, Tesla’s adaptive Kanban system minimized disruptions, allowing it to meet ambitious delivery goals. Additionally, Tesla integrates AI with its Kanban systems, further enhancing predictive supply management and efficiency.
Coca-Cola applies Kanban to ensure consistency in its beverage production and distribution. The company uses Kanban cards to manage raw material levels, such as concentrate and packaging. This process ensures just-in-time replenishment, minimizing overproduction and waste.
For example, during seasonal spikes in demand, Coca-Cola uses Kanban to ramp up production efficiently without overstocking materials. By adopting Kanban, Coca-Cola has achieved faster reaction times to market needs while ensuring high-quality standards. Moreover, the system supports sustainability efforts by reducing wastage and optimizing resource usage.
Samsung utilizes Kanban in electronics manufacturing to synchronize tasks like circuit assembly and quality assurance. The system improves inventory management by providing real-time updates on material availability, such as memory chips or display panels. For example, Samsung uses Kanban to streamline the production of its Galaxy smartphones, reducing delays in assembly.
The approach ensures that components are readily available while avoiding overstocking, leading to lower costs and faster delivery. Samsung has also integrated its Kanban system with IoT devices, providing real-time monitoring and predictive analytics for better resource planning.
Ford employs Kanban to support its lean manufacturing processes, focusing on efficiency and waste reduction. Assembly lines for popular models like the Mustang use Kanban boards to track material usage, ensuring timely replenishment. For instance, Ford monitors tire inventories and triggers automatic restocking when levels fall below a threshold.
This approach eliminates downtime and prevents overproduction, enabling Ford to deliver vehicles efficiently while maintaining profitability. Ford also employs digital Kanban boards to enhance cross-departmental collaboration and improve communication across its global manufacturing units.
Intel uses Kanban to optimize workflows in semiconductor development, balancing complexity and precision. Kanban boards are employed during chip design and testing, helping teams prioritize critical tasks and manage WIP limits. For example, during the creation of its Alder Lake processors, Intel used Kanban to coordinate tasks across design, testing, and production teams.
This approach reduced lead times and improved task alignment, enabling Intel to meet market demand for high-performance processors in a competitive timeframe. Furthermore, Intel has integrated AI-based forecasting with its Kanban system, further improving task accuracy and resource allocation.
Toyota’s introduction of Kanban revolutionized automotive manufacturing, ensuring material availability in its Just-In-Time (JIT) system. The company uses visual Kanban cards to signal supply needs, minimizing inventory levels and reducing waste. For instance, when brake components reach a low threshold, Kanban cards trigger immediate restocking.
This system has enabled Toyota to achieve unparalleled production efficiency, maintain flexibility, and quickly adapt to changing customer demands, setting a global benchmark for lean manufacturing. Toyota’s continuous refinement of Kanban has inspired its use in industries beyond automotive, solidifying its role as a global leader.
Amazon applies Kanban to its logistics and supply chain, ensuring efficient order fulfillment. Fulfillment centers use Kanban boards to track inventory levels and initiate restocking of high-demand items. For example, during Black Friday sales, Amazon’s Kanban system ensures products are replenished promptly to meet surges in demand.
This real-time adaptability allows Amazon to maintain its rapid delivery promise, reduce storage costs, and offer a seamless shopping experience to customers worldwide. Additionally, Amazon uses data-driven Kanban to optimize storage and shipping routes, improving overall efficiency and sustainability.
Boeing integrates Kanban into its aerospace production processes, managing tasks like material procurement and assembly. Kanban boards provide visibility into workflows for complex projects like the 787 Dreamliner. For instance, during component shortages, Boeing uses Kanban signals to prioritize critical supplies, avoiding delays.
This system has enhanced Boeing’s ability to deliver high-quality aircraft on time, even in challenging supply chain environments. Boeing also uses digital dashboards linked to its Kanban system, offering real-time insights and enabling quicker decision-making on production lines.
Google employs Kanban to manage software development workflows across its diverse product portfolio. For example, during updates to Google Search, teams use Kanban boards to prioritize tasks, track bugs, and ensure timely feature rollouts. This system fosters collaboration, aligning teams toward common goals while accommodating changes in project scope.
Google’s agile approach, supported by Kanban, allows it to innovate continuously and maintain leadership in the tech industry. Additionally, Kanban enhances transparency, ensuring all team members have a clear understanding of project progress and priorities.
Apple incorporates Kanban into its design and production workflows for seamless coordination. For instance, during the development of the latest iPhone, Kanban tracks hardware assembly and software updates simultaneously.
This integration ensures tasks are completed in harmony, avoiding delays. Kanban boards provide visibility into progress, enabling proactive issue resolution. Apple’s use of Kanban has been key to maintaining its high standards for innovation and delivering products that set industry benchmarks. Moreover, Apple leverages Kanban to align cross-functional teams, ensuring smooth transitions between hardware and software launches.
Kanban and Just-In-Time (JIT) manufacturing are two complementary systems that work together to optimize production efficiency, reduce waste, and align manufacturing processes with customer demand. JIT aims to minimize inventory by producing only what is needed when it is needed, avoiding the costs of excess stock and overproduction.
Kanban, a visual scheduling system, supports JIT by signaling the need for material replenishment at the right moment, thus ensuring smooth and efficient production flows. By adopting both systems, companies can improve product quality, reduce lead times, and lower costs, all while maintaining flexibility and responsiveness to market changes.
Both Kanban and JIT work together to ensure that production is demand-driven, minimizing delays and ensuring that resources are used effectively. In JIT, materials and products are only made or ordered when needed, reducing waste and the risk of overproduction. Kanban complements JIT by visualizing the process, helping teams easily track inventory levels, manage workloads, and prevent bottlenecks in production. Below is a comparison between Kanban and JIT manufacturing to highlight their interrelationship and benefits.
Kanban is widely used in manufacturing to optimize workflow, reduce waste, and enhance operational efficiency. By visually managing tasks and controlling inventory, Kanban enables manufacturers to achieve smoother production processes, minimize downtime, and improve team collaboration.
Its practical applications help manufacturers respond quickly to changing demands, optimize resource utilization, and improve product quality. Below are the key benefits of using Kanban in manufacturing:
While Kanban offers significant advantages in manufacturing, its implementation can also present several challenges. These challenges can arise from issues related to team coordination, adapting the system to specific manufacturing environments, and maintaining consistent workflows.
Understanding and overcoming these challenges is crucial to ensure that Kanban delivers its intended benefits, such as improved efficiency and reduced waste. Below are some of the common challenges manufacturers may face when using Kanban:
Kanban is a powerful system for managing workflows, originally developed in the manufacturing industry and now widely used in various sectors, including software development, healthcare, and project management.
The system uses visual cues, such as Kanban boards and cards, to track the progress of work, ensuring that tasks are completed efficiently. There are three main types of Kanban: Manufacturing Kanban, Software Development Kanban, and Personal Kanban.
Each type is tailored to meet the needs of different industries and project management scenarios. Still, all are grounded in the same principles of flow, continuous improvement, and work-in-progress (WIP) limits. Below is a detailed exploration of each type of Kanban, focusing on their unique applications and benefits.
Manufacturing Kanban is the original type of Kanban, introduced by Toyota to streamline its production process. This system uses visual signals, such as cards, to trigger the replenishment of materials along the production line. For example, when a component like an engine part runs low, a Kanban card is sent to the supplier to replenish it. By focusing on reducing excess inventory and minimizing waste, Manufacturing Kanban ensures that production runs smoothly and efficiently.
The key benefit of this type is its ability to align material supply with actual production needs, ensuring that there is neither an overstock nor stockout. This results in cost savings, faster production cycles, and a leaner operation. Manufacturing Kanban’s main goal is to promote Just-in-Time (JIT) manufacturing, which allows companies to produce only what is needed when it’s needed.
Software Development Kanban adapts the principles of Kanban for managing tasks and workflows in software projects. Development teams use this type of Kanban to track the progress of tasks such as feature development, bug fixes, or code reviews. In Software Development Kanban, teams use digital Kanban boards to visualize the status of tasks, with columns representing different stages such as “Backlog,” “In Progress,” and “Done.”
The focus of Software Development Kanban is to limit WIP and ensure smooth flow between tasks. It is highly adaptable and encourages continuous improvement through regular reviews of the board to identify bottlenecks or inefficiencies. Unlike Scrum, which is based on sprints, Software Development Kanban allows for continuous delivery, making it suitable for teams that need to adapt quickly to changing requirements. It’s particularly useful in environments where tasks and priorities change frequently, and teams need to be highly responsive to market or customer needs.
Personal Kanban is a simplified version of Kanban used by individuals to manage their tasks and projects. This type of Kanban is ideal for personal productivity and helps people visualize their to-do lists, track progress, and prioritize work. A Personal Kanban board typically includes columns such as “To-Do,” “In Progress,” and “Done.” The system emphasizes limiting WIP to prevent individuals from taking on too many tasks at once, which can lead to burnout or inefficiency.
It encourages individuals to focus on completing one task before starting another, promoting productivity and reducing stress. Personal Kanban can be applied to any area of personal life, whether it's work-related tasks, personal projects, or daily household chores. By making work visible and manageable, individuals can gain clarity on their tasks, ensure they’re not overwhelmed, and experience a sense of accomplishment as they complete tasks. Personal Kanban is especially effective for managing both short-term tasks and long-term goals.
A manufacturing Kanban board is a key tool used to manage workflows in a production environment visually. It helps track the status of work items as they move through different stages of the production process. The board ensures that tasks are completed efficiently and on time while reducing waste and unnecessary delays. By using Kanban boards, manufacturers can enhance visibility, streamline operations, and ensure that the right materials and resources are available when needed. Typically, a Kanban board is divided into multiple columns representing the stages of production, such as "To Do," "In Progress," "Quality Check," and "Completed."
Each task or work item is represented by a card that moves across the board as the task progresses. This real-time tracking allows teams to see the exact status of production, identify bottlenecks, and prioritize work. The Kanban system also encourages continuous improvement, as it highlights inefficiencies and areas for enhancement. Kanban boards are also essential for managing inventory in a pull-based system, where production is triggered based on actual demand rather than forecasts.
This system helps maintain optimal inventory levels, ensuring materials are available when needed without overstocking. Manufacturers can use Kanban boards for better coordination across departments, as it promotes transparency and facilitates communication between production, quality control, and logistics teams. In this way, Kanban boards significantly improve the overall efficiency and performance of the manufacturing process.
Kanban originated in Japan in the late 1940s as a revolutionary method for managing production and inventory, initially developed by Taiichi Ohno at Toyota. Ohno, an engineer at Toyota, sought to improve the company’s manufacturing process and reduce waste by introducing a new approach to inventory management. Inspired by the way supermarkets restocked shelves based on customer demand, Kanban allowed Toyota to implement a just-in-time (JIT) production system, ensuring that parts were only produced or replenished when needed.
This shift significantly reduced inventory costs and waste, contributing to Toyota's rise as a leader in the automotive industry. The Kanban system was first used within Toyota’s factory floor, where it was applied to track the flow of parts from suppliers to assembly lines. It quickly proved to be an effective solution for reducing bottlenecks and ensuring that production was streamlined, efficient, and responsive to customer demand. This new system was part of the larger Toyota Production System (TPS), which revolutionized manufacturing by focusing on efficiency, quality, and the elimination of waste.
By the early 1970s, Kanban had helped Toyota reduce inventory by up to 50%, improving overall operational efficiency. Over the following decades, Kanban’s success at Toyota caught the attention of manufacturers around the world. Companies across various industries embraced its principles, and the system was eventually adapted for software development, project management, and other fields. Today, Kanban continues to be a key method for improving workflows, reducing waste, and optimizing processes in many sectors globally.
Implementing a Kanban system in Lean Manufacturing involves more than just adopting a set of tools; it requires a strategic approach to enhancing workflow efficiency, minimizing waste, and aligning production with actual demand.
Kanban is a visual system that helps manage the flow of materials and tasks throughout the manufacturing process. The implementation of this system aims to streamline processes, reduce bottlenecks, and ensure that resources are allocated effectively.
By introducing a Kanban system as part of Lean Manufacturing, companies can enhance their operational capabilities, reduce waste, and increase overall productivity. Below are the six essential steps to implement Kanban effectively in Lean Manufacturing.
Before implementing Kanban, it’s critical to gain a deep understanding of the entire process flow within the organization. This means mapping out each step in the manufacturing cycle, from raw material procurement to product completion. Teams should carefully observe and document how products, materials, and tasks move through each stage.
By fully understanding the current process, inefficiencies, bottlenecks, or delays can be identified and addressed during the implementation of the Kanban system. With a thorough grasp of how each step interconnects, it will be easier to visualize and manage the flow using Kanban boards, creating a continuous and optimized workflow.
Real-time feedback is a vital component of the Kanban system, ensuring that any changes or disruptions in production are immediately addressed. By using feedback loops, teams can identify when resources, materials, or tasks are lagging behind schedule or when work is being held up. This real-time data should be fed back into the Kanban system, ensuring that necessary adjustments are made swiftly.
For instance, if a specific part or component is delayed, the Kanban board is updated to reflect the issue, and the team can take appropriate actions to resolve the delay. Real-time feedback enables a more agile production process and ensures that the Kanban system continuously adapts to evolving conditions on the shop floor.
In Lean Manufacturing, the effective allocation of resources is essential. The Kanban system allows for a flexible strategy where resources can be allocated dynamically based on real-time demand. By utilizing Kanban boards, managers can visually allocate resources, such as labor or machinery, to areas that need immediate attention, ensuring that no resources are idle or underutilized.
For instance, if one part of the production line is lagging, resources can be temporarily shifted to that area to keep the flow moving. This strategy minimizes waste by ensuring resources are used efficiently and only when needed, aligning with the Lean Manufacturing goal of reducing unnecessary expenditure and improving overall efficiency.
A critical component of Kanban’s success in Lean Manufacturing is fostering cross-functional collaboration between departments. Implementing a Kanban system requires that various teams — including production, procurement, and logistics — communicate effectively. By ensuring all teams have visibility into the workflow and understanding the status of each process, it becomes easier to collaborate and address issues proactively.
For example, suppose there is a delay in receiving raw materials. In that case, the procurement team can take immediate action to ensure materials arrive on time while the production team adjusts the schedule accordingly. By fostering this kind of collaboration, organizations can eliminate silos and improve the flow of information, ensuring smoother production and faster problem resolution.
To take full advantage of the Kanban system in Lean Manufacturing, integrating digital Kanban tools can significantly improve visibility and streamline communication. While traditional Kanban uses physical cards or boards, digital tools provide real-time updates, automate notifications, and allow remote teams to collaborate seamlessly. These tools also offer greater scalability and flexibility, which is especially useful for larger manufacturing operations.
For instance, a company operating multiple plants can use a centralized digital Kanban system to monitor and manage inventory levels and production schedules across all locations. By utilizing digital Kanban tools, organizations can track performance data more efficiently, make better data-driven decisions, and enhance overall coordination.
The last step in implementing Kanban within Lean Manufacturing is to measure performance and continuously improve the system. Success isn’t simply about setting up the Kanban board but about evaluating its impact on production efficiency. Key performance indicators (KPIs) such as cycle time, throughput, and inventory turnover should be tracked regularly to determine how well the Kanban system is functioning.
Once the system is in place, regular reviews should be conducted to identify areas for improvement, refine processes, and make adjustments as needed. Continuous improvement, or Kaizen, is a central philosophy in Lean Manufacturing and should be applied to the Kanban system as well. By constantly assessing and optimizing the Kanban workflow, businesses can ensure long-term efficiency gains and maintain a competitive edge in the market.
Kanban plays a transformative role in the manufacturing sector by enhancing efficiency, reducing waste, and aligning production with real-time demand. Originating from the Toyota Production System, it has become a cornerstone for modern manufacturing practices.
Kanban empowers manufacturers to visualize workflows, streamline operations, and respond promptly to changes in demand. Its adaptability and efficiency make it invaluable for industries looking to optimize processes and meet customer expectations effectively.
Kanban provides a practical and effective method for streamlining manufacturing processes by focusing on demand-driven workflows, visual management, and continuous improvement. It transforms production by ensuring tasks move efficiently through each stage, reducing waste and aligning output with real-time demand.
A typical Kanban process involves using physical or digital Kanban boards and cards to monitor the progress of materials and tasks, ensuring visibility and collaboration across the production floor.
This practical framework helps manufacturers adapt quickly to changing demands, minimize inventory levels, and optimize resource utilization. Here’s how the process works step-by-step in a real-world manufacturing setup:
Kanban in manufacturing has proven to be a transformative approach, optimizing workflows, reducing waste, and improving overall efficiency. By visualizing the entire production process, Kanban enables manufacturers to manage inventory effectively, align production with customer demand, and eliminate bottlenecks. It supports Just-In-Time (JIT) manufacturing by ensuring that materials and components are available when needed, preventing overproduction and excess inventory.
Through continuous monitoring and adjustment, Kanban helps organizations adapt to changing market conditions, reduce costs, and improve product quality. Overall, Kanban enhances manufacturing performance, making it a vital tool for companies seeking operational excellence.
Copy and paste below code to page Head section
Kanban in manufacturing is a visual scheduling system used to manage workflow, inventory, and production. It helps ensure materials are replenished just in time, reducing waste and optimizing production efficiency. Kanban uses cards or boards to signal the need for more materials, ensuring the right amount of inventory is available when needed.
Kanban improves efficiency by providing clear visibility into the production process and helping teams manage work-in-progress (WIP). By tracking material flow, teams can reduce bottlenecks, minimize overproduction, and maintain steady production. This results in optimized workflows, less idle time, and higher resource utilization.
Yes, Kanban can be applied in various industries, including software development, healthcare, and service industries. It helps manage workflows, track tasks, and optimize processes across diverse sectors, ensuring resources are used effectively, minimizing delays, and increasing productivity.
Kanban cards are used to signal the need for material replenishment in the production process. When inventory or work items reach a predefined limit, a card is sent to signal a reorder or move to the next stage. This system ensures continuous flow without overstocking or shortages.
Kanban is a core component of lean manufacturing, helping to eliminate waste by managing inventory and work-in-progress. By using visual signals, Kanban reduces overproduction, excess inventory, and unnecessary motion, contributing to smoother workflows and more efficient production systems.
Key benefits include better inventory management, reduced lead times, enhanced workflow efficiency, and improved communication among teams. Kanban also helps minimize waste, optimize resource allocation, and ensure that production aligns with actual demand, contributing to cost savings and higher quality.